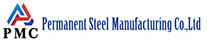
ERW Steel Pipe
ERW Steel Pipe(Electric Resistance Welded Pipe), A53 ERW Pipe, ERW Carbon Steel Pipe, ERW Casing, GI ERW Pipe, Stainless ERW Pipe, ERW Line Pipe
Sizes:
Out Diameter:1/2"-24"
Wall Thickness: 1.65-20mm
Length : 3-12m, or according to customer’s requirement
End : Plain End, Beveled End, Treaded
Standard:
ASTM 5L, ASTM A53, ASTM A135, ASTM A178, ASTM A500/501, ASTM A691, ASTM A252, ASTM A672, EN 10217
Steel Grade:
API 5L: PSL1/PSL2 Gr.A, Gr.B, X42, X46, X52, X56, X60, X65, X70
ASTM A53: GR.A, GR.B
EN: S275, S275JR, S355JRH, S355J2H, S355JOH
GB: Q195, Q215, Q235, Q345, L175, L210, L245, L320, L360-L555
Uses:
For ERW Line Pipe
For ERW Casing
For ERW Structure Tube
For High pressure and high temperature
ERW pipe means Electric Resistance Welded Pipe. Which is manufactured by cold-forming a sheet of steel into a cylindrical shape.
Surface: Lightly oiled, Hot dip galvanized, Electro galvanized, Black, Bare, Varnish coating/Anti rust oil, Protective Coatings (Coal Tar Epoxy, Fusion Bond Epoxy, 3-layers PE)
Packing: Plastic plugs in both ends, Hexagonal bundles of max. 2,000kg with several steel strips, Two tags on each bundle, Wrapped in waterproof paper, PVC sleeve, and sackcloth with several steel strips, Plastic caps.
Test: Chemical Component Analysis, Mechanical Properties (Ultimate tensile strength, Yield strength, Elongation), Technical Properties (Flattening Test, Bending Test, Hardness Test, Impact Test), Exterior Size Inspection, Hydrostatic Test, NDT TEST ( ET TEST, RT TEST, UT TEST)
Small diameter ERW steel pipe
Out diameter | Sch 5 | Sch 10 | Sch 40 | ||||
Inch | mm | Thickness | Kg/mtr |
Thickness |
Kg/mtr |
Thickness |
Kg/mtr |
1/2" | 21.3 | 1.65 | 0.81 | 2.11 | 1.01 | 2.77 | 1.29 |
3/4" | 26.7 |
1.65 |
1.03 | 2.11 | 1.30 | 2.87 | 1.71 |
1" | 33.4 |
1.65 |
1.31 | 2.77 | 2.12 | 3.38 | 2.54 |
1 1/4" | 42.2 |
1.65 |
1.93 | 2.77 | 3.15 | 3.68 | 4.11 |
1 1/2" | 48.3 |
1.65 |
1.93 | 2.77 | 3.15 | 3.68 | 4.11 |
2" | 60.3 |
1.65 |
2.42 | 2.77 | 3.98 | 4.81 | 5.31 |
3" | 88.9 | 2.11 | 4.58 | 3.05 | 6.54 | 5.49 | 11.45 |
3 1/2" | 101.6 | 2.11 | 5.25 | 3.05 | 7.52 | 5.74 |
13.77 |
4" | 114.3 | 2.11 | 5.25 | 3.05 | 7.52 | 5.74 | 13.77 |
5" | 141.3 | 2.77 | 9.50 | 3.40 | 11.74 | 6.55 | 22.10 |
6" | 168.3 | 2.77 | 11.47 | 3.40 | 14.04 | 7.11 | 28.68 |
8" | 219.1 | 2.77 | 14.99 | 3.76 | 20.25 | 8.18 | 43.16 |
OD | WT | ||||||||
Inch | mm |
8 5/8" |
219.1mm |
10 3/4" |
273.1mm |
12 3/4" |
325.0mm |
14" |
355.6mm |
0.157 | 4.0 |
|
|
|
|
|
|
|
|
0.197 | 5.0 |
|
|
|
|
|
|
|
|
0.236 | 6.0 |
|
|
|
|
|
|
|
|
0.276 | 7.0 |
|
|
|
|
|
|
|
|
0.315 | 8.0 |
|
|
|
|
|
|
|
|
0.354 | 9.0 |
|
|
|
|
|
|
|
|
0.394 | 10.0 |
|
|
|
|
|
|
|
|
0.133 | 11.0 |
|
|
|
|
|
|
|
|
0.492 | 12.5 |
|
|
|
|
|
|
|
|
0.551 | 14.0 |
|
|
|
|
|
|
|
|
0.630 | 16.0 |
|
|
|
|
|
|
|
|
0.689 | 17.5 |
|
|
|
|
|
|
|
|
0.748 | 19.0 |
|
|
|
|
|
|
|
|
0.787 | 20.0 |
|
|
|
|
|
|
|
|
OD | WT | ||||||||||
Inch | mm |
16" |
406.4mm |
18" |
457.7mm |
20" |
508.0mm |
24" |
610mm |
24 4/5" |
630.0mm |
0.157 | 4.0 |
|
|
|
|
|
|
|
|
|
|
0.197 | 5.0 |
|
|
|
|
|
|
|
|
|
|
0.236 | 6.0 |
|
|
|
|
|
|
|
|
|
|
0.276 | 7.0 |
|
|
|
|
|
|
|
|
|
|
0.315 | 8.0 |
|
|
|
|
|
|
|
|
|
|
0.354 | 9.0 |
|
|
|
|
|
|
|
|
|
|
0.394 | 10.0 |
|
|
|
|
|
|
|
|
|
|
0.133 | 11.0 |
|
|
|
|
|
|
|
|
|
|
0.492 | 12.5 |
|
|
|
|
|
|
|
|
|
|
0.551 | 14.0 |
|
|
|
|
|
|
|
|
|
|
0.630 | 16.0 |
|
|
|
|
|
|
|
|
|
|
0.689 | 17.5 |
|
|
|
|
|
|
|
|
|
|
0.748 | 19.0 |
|
|
|
|
|
|
|
|
|
|
0.787 | 20.0 |
|
|
|
|
|
|
|
|
|
|
ERW Pipe Manufacturering Process:
Straight seam high frequency welded pipe (ERW steel pipe) is formed by forming a hot-rolled coil through a forming machine. The skin effect and proximity effect of high-frequency current are used to heat and melt the edge of the pipe blank. Pressure welding is produced under the action of squeeze rollers. Welded steel pipes have simple production process, high production efficiency, many varieties and specifications, and less equipment, but their general strength is lower than seamless steel pipes.
1. Uncoiling --- 2. Leveling --- 3. End cutting --- 4. End shearing welding --- 5. Supercoil accumulator --- 6. Edge cutting --- 7. Ultrasonic detection --- 8. Forming --- 9. Electric induction welding --- 10. Ultrasonic detection for weld seam --- 11. Medium frequency heat treatment --- 12. Air cooling --- 13. Water cooling --- 14. Sizing --- 15. Flying cutting --- 16. Flush-out --- 17. Cropping --- 18. Flattening testing --- 19. Straightening --- 20. End facing and bevelling --- 21. Hydrodynamic testing --- 22. Ultrasonic detection for weld seam --- 23. Ultrasonic detection for pipe end --- 24. Visual and dimensions inspection --- 25. Weighting and measuring --- 26. Marking --- 27. Coating --- 28. Pipe-end protection --- 29. Bending --- 30. Shipping
The ERW steel pipe/tube production line is the world's first non-destructive testing technology, with advanced forming technology, high-power welding, full-featured, double-weld heat treatment and full-tube heat treatment equipment, as well as a computerized logistics tracking system throughout the process. The integrated medium diameter straight seam welded pipe production equipment is one of the most advanced welded pipe production lines in the world. The main equipment is provided by the world's most advanced straight seam welded pipe equipment manufacturers such as German SMS and MEER, with an annual output of 300,000 tons of line pipes. Straight seam welded pipe products such as erw casing, structural pipe (round pipe, rectangular pipe).