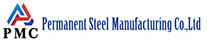
LSAW Steel Pipe
LSAW Steel Pipe (Longitudinally Submerged Arc Welded Pipe) , DSAW Steel Pipe, SAWL Steel Pipe
Straight Seam Submerged Arc Welded Steel Pipe
UOE SAWL PIPES
Outside Diameter:Φ508mm- 1118mm (20"- 44")
Wall Thickness: 6.0-25.4mm 1/4"-1"
JCOE SAWL PIPES
Outside Diameter:Φ406mm- 1626mm (16" - 64" )
Wall Thickness:6.0- 75mm (1/4" - 3" )
Quality Standards:API、DNV、ISO、DEP、EN、ASTM、DIN、BS、JIS、GB、CSA
Length:3-12.5m ( 10'- 41' )
Grades:API 5L A-X100, GB/T9711 L190-L690
Tolerance of Outside Diameter and Wall Thickness
Types |
Standard |
|||||
SY/T5040-2000 |
SY/T5037-2000 |
SY/T9711.1-1977 |
ASTM A252 |
AWWA C200-97 |
API 5L PSL1 |
|
Tube end OD deviation |
±0.5%D |
±0.5%D |
-0.79mm~+2.38mm |
<±0.1%T |
<±0.1%T |
±1.6mm |
Wall thickness |
±10.0%T |
D<508mm, ±12.5%T |
-8%T~+19.5%T |
<-12.5%T |
-8%T~+19.5%T |
5.0mm |
D>508mm, ±10.0%T |
T≥15.0mm, ±1.5mm |
Chemical Composition and Mechanical Properties of LSAW Steel Pipe
Standard |
Grade |
Chemical Composition(max)% |
Mechanical Properties(min) |
|||||
C |
Mn |
Si |
S |
P |
Yield Strength (Mpa) |
Tensile Strength (Mpa) |
||
GB/T700-2006 |
A |
0.22 |
1.4 |
0.35 |
0.050 |
0.045 |
235 |
370 |
B |
0.2 |
1.4 |
0.35 |
0.045 |
0.045 |
235 |
370 |
|
C |
0.17 |
1.4 |
0.35 |
0.040 |
0.040 |
235 |
370 |
|
D |
0.17 |
1.4 |
0.35 |
0.035 |
0.035 |
235 |
370 |
|
GB/T1591-2009 |
A |
0.2 |
1.7 |
0.5 |
0.035 |
0.035 |
345 |
470 |
B |
0.2 |
1.7 |
0.5 |
0.030 |
0.030 |
345 |
470 |
|
C |
0.2 |
1.7 |
0.5 |
0.030 |
0.030 |
345 |
470 |
|
BS En10025 |
S235JR |
0.17 |
1.4 |
- |
0.035 |
0.035 |
235 |
360 |
S275JR |
0.21 |
1.5 |
- |
0.035 |
0.035 |
275 |
410 |
|
S355JR |
0.24 |
1.6 |
- |
0.035 |
0.035 |
355 |
470 |
|
DIN 17100 |
ST37-2 |
0.2 |
- |
- |
0.050 |
0.050 |
225 |
340 |
ST44-2 |
0.21 |
- |
- |
0.050 |
0.050 |
265 |
410 |
|
ST52-3 |
0.2 |
1.6 |
0.55 |
0.040 |
0.040 |
345 |
490 |
|
JIS G3101 |
SS400 |
- |
- |
- |
0.050 |
0.050 |
235 |
400 |
SS490 |
- |
- |
- |
0.050 |
0.050 |
275 |
490 |
|
API 5L PSL1 |
A |
0.22 |
0.9 |
- |
0.03 |
0.03 |
210 |
335 |
B |
0.26 |
1.2 |
- |
0.03 |
0.03 |
245 |
415 |
|
X42 |
0.26 |
1.3 |
- |
0.03 |
0.03 |
290 |
415 |
|
X46 |
0.26 |
1.4 |
- |
0.03 |
0.03 |
320 |
435 |
|
X52 |
0.26 |
1.4 |
- |
0.03 |
0.03 |
360 |
460 |
|
X56 |
0.26 |
1.1 |
- |
0.03 |
0.03 |
390 |
490 |
|
X60 |
0.26 |
1.4 |
- |
0.03 |
0.03 |
415 |
520 |
|
X65 |
0.26 |
1.45 |
- |
0.03 |
0.03 |
450 |
535 |
|
X70 |
0.26 |
1.65 |
- |
0.03 |
0.03 |
585 |
570 |
LSAW Steel Pipe Manufacturing Process:
LSAW steel pipe (Longitudinally Submerged Arc Welding abbreviated as LSAW) is a professional expression term for LSAW steel pipe. It uses a single medium and thick plate as the raw material, and the steel plate is pressed (rolled) into a tube blank in a mold or a forming machine. The pipe is produced by submerged arc welding and expanded diameter.
UOE LSAW pipe forming process:
The three main forming processes of UOE LSAW steel pipe forming process include: steel plate pre-bending, U forming and O forming. Each process adopts a dedicated forming press to complete the three processes of pre-bending the edge of the steel plate, U forming and O forming in sequence to deform the steel plate into a circular tube.
JCOE LSAW pipe forming process:
Forming: After several steps of stamping on the JCO forming machine, first half of the steel plate is pressed into a "J" shape, then the other half of the steel plate is pressed into a "J" to form a "C" shape, and finally pressurized from the middle to form An open "O"-shaped tube blank is formed.
Tests of LSAW steel pipe
Chemical Component Analysis
Mechanical Properties – Elongation, Yield Strength, Ultimate Tensile Strength
Technical Properties – DWT Test, Impact Test, Blow Test, Flattening Test
X-ray Test
Exterior Size Inspection
Hydrostatic Test
UT Test
Transportation of LSAW steel pipe
When transporting, loading and unloading lsaw welded pipes, special hoisting and transportation tools should be used to avoid scratching the surface.
Production equipment of LSAW steel pipe
Plate edge milling machine
The milling machine mills the two sides of the plate to exacting standards in order to meet width, edging and groove shape specifications.
Edge crimping machine
The crimping machine crimps the edges of the plate to form the required curvature.
Tack welding machine
The two edges of the open seam pipe are brought together by the tack welding machine. then welded by the tack welder using a metal active - gas arc welding("MAG" )process.
Forming machine
Utilizes the "JCO" process to bend and form the crimped steel plate into a steel pipe.
Interior welding machine
The interior longitudinal seam of the pipe is welded from the inside by fixing 4 welding heads while moving pipe and using submerged-arc welding process.
End facing machine
The machine levels the pipe end with rotating cutter heads to ensure that required groove and edge specifications are met.
Hydrostatic tester
Using end face sealing technology eliminates blind zones during hydrostatic testing. The tester is also equipped with automatic recording and storing functions.
Expanding machine
The pipe is subjected to full-length expansion to increase the precision of the pipe dimensions and to improve the internal stress distribution.
Automated ultrasonic testing equipment
The superiority of phased arrayultra sonic technology:
(1 )Adopting electron control method for fast linear scanning or sector scanning without moving probe or moving less. thus greatlyim prove detection efficiency.
(2)Controlting the sound beam by setting detection angles, its good sound beam reachability can enhances reliability and accuracy of detection.
(3) Dynamic control the deflection and focus of sound beam realizes the detection of pipes with different wall thickness without replacing probes.