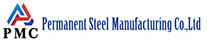
ERW stands for “electric resistance welded”. ERW pipes and tubes are manufactured by rolling metal and then welding it longitudinally across its length. ERW pipes have a welded joint in their cross-section. ERW pipe cold formed from a ribbon of steel pulled through a series of rollers and formed into a tube which is fused through an electric charge. It is mainly used for low/ medium pressure applications such as the transportation of water /oil.
Pipeline transportation is a mode of transportation that uses pipelines as a means of transportation and is driven by a certain pressure difference to transport fluid substances such as gas, liquid, slurry (such as oil, natural gas, water, coal slurry, etc.) over long or short distances. It has the characteristics of strong continuity, high transportation efficiency, low energy consumption, and little impact on the natural environment. It is one of the five major transportation modes in the modern logistics system, along with railways, highways, waterways, and aviation. It occupies a core position in the transportation of energy such as oil and natural gas, especially.
Advantages of ERW Pipe In Pipeline Transportation
ERW (high frequency electric resistance welding) steel pipes have shown a number of irreplaceable advantages in the field of pipeline transportation (covering oil, gas, water, chemical media and other transportation scenarios) due to their unique production process and performance characteristics, as follows:
1. Stable welding quality and high overall strength
ERW steel pipes use high-frequency current to heat the edge of the pipe, causing it to fuse under pressure. The metal grains at the weld are recrystallized, and the weld strength is close to that of the parent material, avoiding defects such as pores and slag inclusions that may occur in traditional welding.
This uniform welding quality ensures that the pipeline can withstand higher working pressures (especially suitable for medium and high pressure transportation scenarios), reduces the risk of leakage caused by weak welds during long-distance transportation, and ensures the safety of medium transportation.
2. High dimensional accuracy and strong consistency
The production process is controlled by precision rolling mills, so the outer diameter and wall thickness deviations of ERW steel pipes are small, and the roundness and straightness are highly accurate.
This feature makes it easier to connect pipes (such as welding and flange connections), reduces installation errors, and improves construction efficiency; at the same time, the uniform size helps to reduce the flow resistance of the medium and reduce transportation energy consumption.
3. High production efficiency and significant cost advantage
The ERW process involves continuous rolling and welding, which is simpler than the perforation and rolling process of seamless steel pipes, with fast production speed and high yield rate (the utilization rate of raw materials can reach more than 90%).
The lower production cost makes it more economical in large-diameter, medium- and low-pressure pipeline projects. It is especially suitable for large-scale laying of long-distance transmission pipelines (such as urban water supply networks, oil and gas branch pipelines), which can significantly reduce the total project investment.
4. Strong adaptability and wide range of specifications
ERW steel pipes can be produced in a wide range of specifications, from small and medium diameters (such as DN15) to larger diameters (some processes can reach DN600 or above), and can be stably produced, and the wall thickness can be flexibly adjusted according to the delivery pressure requirements.
It can not only meet the small and medium-caliber branch transportation of urban pipelines, but also adapt to the medium-caliber requirements of long-distance trunk pipelines. It is suitable for the transportation scenarios of various media (oil, gas, water, steam, etc.).
5. Excellent corrosion resistance and fatigue resistance
After surface treatment (such as galvanizing and anti-corrosion coating), high-quality ERW steel pipes have enhanced resistance to soil corrosion and atmospheric corrosion, especially in underground water and gas pipelines, which can extend their service life and reduce maintenance costs.
In addition, its uniform material and structure give it good fatigue resistance, can adapt to pressure fluctuations during medium transportation, and reduce the risk of cracking after long-term use.
6. Environmental protection and sustainability are outstanding
Compared with seamless steel pipes, the ERW process consumes less energy (no high-temperature perforation is required), emits less pollutants during the production process, and meets the environmental protection requirements of modern industry.
At the same time, steel pipes can be recycled and reused. After the pipelines are retired, they can be reprocessed through smelting, reducing resource waste and conforming to the trend of green pipeline construction.
These advantages make ERW steel pipes the preferred pipe material with both cost-effectiveness and reliability in pipeline transportation fields such as urban infrastructure (water supply, heating, gas), oil and gas field gathering and transportation, and chemical media transportation.
Read more: Advantages and Disadvantages of Pipeline Transportation