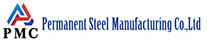
Large diameter seamless pipes are typically used in industries where high strength, reliability, and performance under pressure are critical. These pipes are preferred over welded pipes when it comes to applications that involve high-pressure fluids or gases, as the absence of a seam reduces the risk of failure along a weld. Large diameter seamless pipes are widely used in social development and are involved in many construction projects. Therefore, the welding process is particularly important for large diameter seamless pipes.
So let's take a look at the precautions for the welding process of large diameter seamless pipes.
1. Set up wind, rain and snow shelters at the welding site on windy, rainy and snowy days.
2. The ice and snow inside and outside the welded pipe mouth and the moisture near the weld should be wiped dry or dried.
3. Strictly follow the operating procedures.
4. When welding large-diameter seamless pipes and components, the welding rods and wires should be dried and insulated, and stored in an insulation tube for easy use.
5. When the temperature of the pipeline welding part is lower than 0 degrees Celsius, all steel parts and welds should be preheated to above 15 degrees Celsius within 100 mm of the starting welding point. The preheating method adopts the method of building a scaffold, making a fire and gas welding local heating.
6. In winter, it is necessary to increase the current while heating during the welding process, and to cover the insulation felt after welding to reduce the temperature gradient of the weld area.
What are the methods for forming large diameter seamless pipes?
1. Hot piercing rolling method for large diameter seamless pipes
Hot piercing rolling is mainly longitudinal rolling and diagonal rolling. Longitudinal rolling and extension rolling mainly include limited mandrel continuous tube rolling, limited mandrel continuous tube rolling with few stands, three-roller limited mandrel continuous tube rolling and floating mandrel continuous tube rolling. These methods have low production, low metal consumption, good product quality, and control system, and are increasingly widely used.
2. Hot push expansion method for large diameter seamless pipes
Push expansion equipment is simple, inexpensive, easy to maintain, economical, and flexible in product specifications. If you need to prepare large-diameter seamless pipes and other similar products, you only need to add some accessories. It is suitable for the production of medium- and thin-walled large-diameter seamless pipes, and can also produce thick-walled pipes that do not exceed the equipment capacity.
3. Hot extrusion method for large diameter seamless pipes
Before extrusion, the blank needs to be pre-processed by machining. When extruding pipes with a diameter of less than 100 mm, the equipment investment is small, the material waste is small, and the technology is relatively mature. However, once the diameter of the pipe increases, the hot extrusion method requires large-tonnage and high-power equipment, and the corresponding control system must also be upgraded.
Causes and adjustments for uneven wall thickness of steel pipes
1. Causes of uneven wall thickness at the head and tail: The front end of the tube billet is cut with a large inclination, the curvature is too large, and the centering hole of the tube billet is not straight, which can easily cause uneven wall thickness at the head of the steel pipe. The elongation coefficient is too large during perforation, the roll speed is too high, and the rolling is unstable. The unstable steel throwing of the perforator can easily cause uneven wall thickness at the tail of the rough tube.
Measures: Check the tube billet to prevent the front end of the tube billet from cutting at an angle or with a large amount of pressure reduction. The centering hole should be corrected when changing the hole type or overhauling. Use a lower piercing speed to ensure rolling stability and uniformity of rough tube wall thickness. When the roll speed is adjusted, the matching guide plate should also be adjusted accordingly. Pay attention to the use status of the guide plate and increase the inspection of the guide plate bolts to reduce the movement of the guide plate during steel rolling and ensure stable steel throwing.
2. The causes of spiral wall thickness unevenness are: uneven wall thickness caused by the piercing machine rolling center line is not straight, the inclination angles of the two rollers are not equal, or the amount of pressure before the head is too small, which generally distributes in a spiral shape along the entire length of the steel pipe. Uneven wall thickness caused by premature opening of the centering roller, improper adjustment of the centering roller, and shaking of the mandrel during the rolling process generally distributes in a spiral shape along the entire length of the steel pipe.
Measures: Adjust the rolling center line of the punching machine to make the inclination angles of the two rollers equal, and adjust the tube rolling mill according to the parameters given in the rolling table. For this situation, adjust the opening time of the centering roller according to the speed of the raw tube inlet and outlet. Do not open the centering roller too early during the rolling process to prevent the top rod from shaking and causing uneven wall thickness. The opening of the centering roller needs to be appropriately adjusted according to the change of the raw tube diameter, and the size of the raw tube runout should be considered.
3. Causes of linear wall thickness unevenness: improper adjustment of the mandrel pre-piercing saddle height, the mandrel contacts the rough tube on one side during pre-piercing, causing the rough tube to cool too quickly on the contact surface, resulting in uneven wall thickness or even concave defects. The gap between the continuous rolling rolls is too small or too large. Deviation of the center line of the tube mill. Uneven reduction of single and double stands. Mortar fracture and large difference in the gap between the inner and outer rolls will cause linear asymmetric deviation of the steel pipe. Improper adjustment of continuous rolling, stacking steel and drawing steel rolling will cause linear wall thickness unevenness.
Measures: Adjust the height of the mandrel pre-saddle and the centering of the mandrel and the rough tube. When changing the hole type and rolling specifications, the roll gap should be measured to keep the actual roll gap consistent with the rolling table. Use the optical centering device to adjust the rolling center line, and calibrate the center line of the tube mill during the annual overhaul. Replace the broken stand in time, measure the inner and outer roll gaps of the continuous rolling rollers, and replace them in time if there are problems. Avoid pulling and piling steel during continuous rolling.
Read more: Large Diameter Seamless Steel Pipe