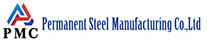
Seamless steel pipe end grinding: After cutting, the plastic layer of the pipe mouth should be polished with an angle grinder to avoid melting or even burning of the plastic layer during flange welding, which may damage the pipe. Use an angle grinder to grind the plastic layer of the pipe mouth.
Plastic coating of seamless steel pipe: After polishing, use oxygen and C2H2 to heat the pipe mouth outside the pipe until the internal plastic layer melts. Then the technicians will evenly apply the prepared plastic powder to the pipe mouth. Pay attention to applying it in place. The flange plastic coating should be applied above the water stop line. The heating temperature should be strictly controlled during this process. If the temperature is too high, bubbles will be generated during the plastic coating process. If the temperature is too low, the plastic powder will melt during the plastic coating process. The above situations will cause the plastic layer to fall off after the pipeline is put into use, and the seamless steel pipe part of the pipeline will be corroded and damaged.
Seamless steel pipe cutting:
According to the actual required pipeline length, the pipeline should be cut with a metal saw or a toothless saw. When using water welding during the cutting process, the raw materials must be protected. When cutting, heat-resistant materials should be used as baffles at both ends of the fracture to catch the sparks and hot iron water beans that fall during cutting, and protect the original plastic layer of the raw materials.
The control of seamless steel pipes is a difficult point in steel pipe production. The measures to improve the precision of seamless steel pipes mainly include the following aspects:
1. Rolling tool installation
The center of the roller pitch and guide distance needs to be on the rolling line.
The center line of the guide pitch and roll pitch is on the center line of piercing and rolling, that is, the upper and lower roll pitches are equal, and the left and right guide pitches are equal.
2. Perforated ejector
The perforated mandrel is generally selected with an outer diameter of Φ108mm-Φ114mm, and the seamless steel pipe is required to be ≥25mm and the seamless steel pipe is uniformly thick-walled.
3. Rolling mill mandrel
The mandrel should be made of thick-walled seamless steel pipe. For mandrels with smaller specifications, solid billets can be used instead. The uniform thick-walled tube and solid billet of seamless steel pipe can greatly reduce the probability of bending and deformation of the mandrel, and can improve the seamless steel pipe accuracy of the steel pipe.
4. The precision of the mandrel
The core rod is relatively long and thin, so it is usually machined first and then welded, or long material is directly turned into shape. The external machining accuracy of the core rod is controlled within ±0.1mm, and the straightness deviation of the core rod does not exceed 5mm. During welding, a precision-machined pin is inserted between the two mandrel sections for positioning to prevent excessive deviation in the total straightness caused by welding.
5. Tube heating
The heating should be uniform, and the temperature should not be raised or lowered. Each temperature rise or fall should be steady and slow, and the maximum temperature rise or fall should not exceed 30℃.
6. Centering roller
Check whether the centering roller is installed in place, adjust the center of the relevant core roller, the opening angle and the opening size of each action to be consistent, and the center of the core roller should be on the rolling line.
7. Rolling center line
The rolling center line of the piercing machine is consistent with the center line of the piercing trolley to avoid "upward rolling" or "downward rolling" so that the tube billet is evenly stressed during piercing.
8. Rolling tools
Worn rolling tools such as top heads, guide plates, rollers, etc. should be replaced in time.
Read more: What are the Cutting Methods of Seamless Steel Pipes?