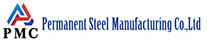
304 stainless steel pipe is a widely used pipe made from 304 stainless steel, an austenitic alloy known for its excellent corrosion resistance, durability, and versatility.
Its composition contains 18% chromium and 8% nickel, used in food production equipment, chemical equipment, nuclear energy, etc.
Types of 304 Stainless Steel Pipes
1. Welded Pipe:
Welded pipes are formed by joining two pieces of stainless steel together through welding. They are typically less expensive than seamless pipes and are used in applications that do not require high pressure or extreme conditions.
2. Seamless Pipe:
Seamless pipes are manufactured by extruding the stainless steel, producing a pipe with no seams or welds. They are stronger and more resistant to pressure compared to welded pipes, making them suitable for critical applications like high-pressure environments or chemical processing.
3. Polished Pipe:
Polished 304 pipes have a smooth, attractive finish and are often used in applications where appearance matters, such as in architectural or decorative projects.
4. Schedule Pipe:
304 stainless steel pipes come in different schedules (or thicknesses), such as Schedule 10, 40, and 80. The schedule determines the wall thickness of the pipe and is chosen based on the pressure and structural requirements of the application.
Acceptance criteria for 304 stainless steel pipe
1. Chemical Composition
The pipe must meet the standard chemical composition for 304 stainless steel as per applicable standards (e.g., ASTM A312, ASME, etc.):
Chromium (Cr): 18.0–20.0%
Nickel (Ni): 8.0–10.5%
Carbon (C): Max 0.08%
Manganese (Mn): Max 2.0%
Phosphorus (P): Max 0.045%
Sulfur (S): Max 0.030%
Silicon (Si): Max 1.0%
Nitrogen (N): Max 0.10%
2. Mechanical Properties
The following mechanical properties are typically required for 304 stainless steel pipes:
Tensile Strength: Minimum 515 MPa (75,000 psi)
Yield Strength (0.2% offset): Minimum 205 MPa (30,000 psi)
Elongation: Minimum 35% for pipes of smaller diameters.
Hardness: Usually measured in Rockwell B or Vickers hardness scale. Max Rockwell B hardness is often limited to 92.
3. Dimensional Tolerances
Pipes must meet specific dimensional tolerances based on relevant standards (e.g., ASTM A269, A312):
Outer Diameter (OD): Tolerances are generally within ±0.5%.
Wall Thickness: Typically within ±10% of the specified nominal thickness.
Length: Tolerances for length can vary depending on whether the pipe is cut to fixed lengths or random lengths.
Ovality: The difference between maximum and minimum OD should be controlled within permissible limits.
4. Surface Finish
Internal and External Surface: Should be free from defects such as cracks, gouges, pits, or visible impurities that may affect performance.
Polishing: For some applications (e.g., sanitary), a specific surface finish may be required (e.g., a No. 4 or 2B finish).
Pickling and Passivation: Post-fabrication treatment processes like pickling and passivation may be required to improve the corrosion resistance of the pipe.
5. Weld Quality
Weld Bead: The welded seam must be smooth, free from defects such as cracks, undercutting, or excessive convexity/concavity.
Non-Destructive Testing (NDT): Welds are often inspected using methods like X-ray or ultrasonic testing to ensure the integrity of the welds.
Fusion: No lack of fusion or incomplete penetration should be present in the weld area.
6. Corrosion Testing
Pipes are sometimes subjected to corrosion resistance tests like the ASTM A262 practice to ensure resistance to intergranular corrosion.
The test may involve exposure to specific chemicals (e.g., nitric acid) to evaluate the pipe's resistance.
7. Hydrostatic Test
The pipe must undergo a hydrostatic test to ensure it can withstand internal pressures without leakage. This is usually performed at 1.5 times the working pressure or a specified minimum pressure based on the pipe's rating.
8. Visual Inspection
The pipe should be visually inspected for any surface imperfections, weld defects, or dimensional inconsistencies.
The pipe should be free from rust, scaling, cracks, or foreign matter.
9. Straightness
The pipe should meet straightness requirements to avoid bowing or twisting, which could impact its performance. Some standards allow for a maximum deviation of 1 mm per meter length or similar tolerances depending on application.
10. Marking and Certification
The pipe must be properly marked with relevant information like:
Grade of material (304 stainless steel)
Heat number or batch identification
Dimensions (OD, wall thickness, length)
Applicable standard (e.g., ASTM A312)
A mill test certificate (MTC) is often required to verify that the material meets the specified requirements.
11. End Preparation
Pipe ends must meet specified requirements:
Plain Ends: Smooth and square to the axis.
Beveled Ends: For welding, ends should be beveled according to the specified angle.
Threaded Ends: If required, threading should meet the relevant standards (e.g., NPT or BSP threading).
Read more: 304 Stainless Steel Pipe Specifications