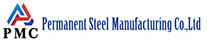
Su composición contiene un 18 % de cromo y un 8 % de níquel, y se utiliza en equipos de producción de alimentos, equipos químicos, energía nuclear, etc.
Tipos de tubos de acero inoxidable 304
1. Tubos soldados:
Los tubos soldados se forman uniendo dos piezas de acero inoxidable mediante soldadura. Suelen ser menos costosos que los tubos sin costura y se utilizan en aplicaciones que no requieren alta presión o condiciones extremas.
2. Tubos sin costura:
Los tubos sin costura se fabrican mediante la extrusión del acero inoxidable, lo que produce un tubo sin costuras ni soldaduras. Son más fuertes y resistentes a la presión en comparación con los tubos soldados, lo que los hace adecuados para aplicaciones críticas como entornos de alta presión o procesamiento químico.
3. Tubería pulida:
Las tuberías 304 pulidas tienen un acabado liso y atractivo y suelen utilizarse en aplicaciones en las que la apariencia es importante, como en proyectos arquitectónicos o decorativos.
4. Tubería de calibre:
Las tuberías de acero inoxidable 304 vienen en distintos calibres (o espesores), como el calibre 10, 40 y 80. El calibre determina el espesor de la pared de la tubería y se elige en función de la presión y los requisitos estructurales de la aplicación.
Criterios de aceptación para tuberías de acero inoxidable 304
1. Composición química
La tubería debe cumplir con la composición química estándar para acero inoxidable 304 según las normas aplicables (p. ej., ASTM A312, ASME, etc.):
Cromo (Cr): 18,0–20,0 %
Níquel (Ni): 8,0–10,5 %
Carbono (C): Máx. 0,08 %
Manganeso (Mn): Máx. 2,0 %
Fósforo (P): Máx. 0,045 %
Azufre (S): Máx. 0,030 %
Silicio (Si): Máx. 1,0 %
Nitrógeno (N): Máx. 0,10 %
2. Propiedades mecánicas
Las siguientes propiedades mecánicas son las que se requieren normalmente para las tuberías de acero inoxidable 304:
Resistencia a la tracción: mínimo 515 MPa (75 000 psi)
Límite de fluencia (desplazamiento del 0,2 %): mínimo 205 MPa (30 000 psi)
Elongación: mínimo 35 % para tuberías de diámetros más pequeños.
Dureza: normalmente se mide en la escala de dureza Rockwell B o Vickers. La dureza máxima Rockwell B suele estar limitada a 92.
3. Tolerancias dimensionales
Las tuberías deben cumplir con tolerancias dimensionales específicas basadas en estándares relevantes (p. ej., ASTM A269, A312):
Diámetro exterior (OD): las tolerancias generalmente están dentro del ±0,5 %.
Espesor de pared: generalmente dentro del ±10 % del espesor nominal especificado.
Longitud: las tolerancias para la longitud pueden variar dependiendo de si la tubería se corta en longitudes fijas o longitudes aleatorias.
Ovalidad: la diferencia entre el OD máximo y mínimo debe controlarse dentro de límites permisibles.
4. Acabado de la superficie
Superficie interna y externa: debe estar libre de defectos como grietas, ranuras, picaduras o impurezas visibles que puedan afectar el rendimiento.
Pulido: para algunas aplicaciones (p. ej., sanitarias), puede requerirse un acabado de superficie específico (p. ej., un acabado N.º 4 o 2B).
Decapado y pasivación: Es posible que se requieran procesos de tratamiento posteriores a la fabricación, como el decapado y la pasivación, para mejorar la resistencia a la corrosión de la tubería.
5. Calidad de la soldadura
Cordón de soldadura: la costura soldada debe ser lisa y no presentar defectos como grietas, socavaduras o convexidad/concavidad excesiva.
Pruebas no destructivas (NDT): las soldaduras suelen inspeccionarse mediante métodos como rayos X o pruebas ultrasónicas para garantizar la integridad de las soldaduras.
Fusión: no debe haber falta de fusión ni penetración incompleta en el área de soldadura.
6. Pruebas de corrosión
En ocasiones, las tuberías se someten a pruebas de resistencia a la corrosión, como la práctica ASTM A262, para garantizar la resistencia a la corrosión intergranular.
La prueba puede implicar la exposición a sustancias químicas específicas (por ejemplo, ácido nítrico) para evaluar la resistencia de la tubería.
7. Prueba hidrostática
La tubería debe someterse a una prueba hidrostática para garantizar que pueda soportar presiones internas sin fugas. Esto se realiza generalmente a 1,5 veces la presión de trabajo o a una presión mínima especificada según la clasificación de la tubería.
8. Inspección visual
La tubería debe inspeccionarse visualmente para detectar imperfecciones en la superficie, defectos de soldadura o inconsistencias dimensionales.
La tubería debe estar libre de óxido, incrustaciones, grietas o materias extrañas.
9. Rectitud
La tubería debe cumplir con los requisitos de rectitud para evitar curvaturas o torsiones, que podrían afectar su rendimiento. Algunas normas permiten una desviación máxima de 1 mm por metro de longitud o tolerancias similares según la aplicación.
10. Marcado y certificación
La tubería debe estar correctamente marcada con información relevante como:
Grado del material (acero inoxidable 304)
Número de colada o identificación del lote
Dimensiones (diámetro exterior, espesor de pared, longitud)
Norma aplicable (p. ej., ASTM A312)
A menudo se requiere un certificado de prueba de fábrica (MTC) para verificar que el material cumple con los requisitos especificados.
11. Preparación de los extremos
Los extremos de la tubería deben cumplir con los requisitos especificados:
Extremos lisos: lisos y en escuadra con el eje.
Extremos biselados: para soldar, los extremos deben estar biselados de acuerdo con el ángulo especificado.
Extremos roscados: si es necesario, la rosca debe cumplir con las normas pertinentes (p. ej., rosca NPT o BSP).
Leer más: Especificaciones de tubos de acero inoxidable 304