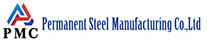
The large diameter welded pipe size usually refers to steel welded pipes with larger diameters. Generally speaking, the size of large diameter welded pipe will vary according to production standards and requirements. The size of large-diameter welded pipes can include diameters from 6 inches to 60 inches, wall thickness usually ranges from 5 mm to 30 mm, and the length can be customized according to customer needs, usually 6 meters, 9 meters or 12 meters, etc. This is just an example, actual dimensions will vary based on production standards, material requirements and usage. The specific size you need can be determined based on your project and needs.
Selecting the appropriate material depends on factors such as the specific use of the large diameter welded pipe, working environment, medium characteristics, and budget.
3. Large diameter welded pipe standards
The production and quality of large-diameter welded pipes generally need to comply with the following international standards and industry standards:
(1) ASTM standards: The American Society for Testing and Materials has formulated a number of welded pipe standards, such as ASTM A53/A53M, ASTM A252, ASTM A139, etc., covering the requirements and uses of welded pipes of different materials and sizes.
(2) API standards: The American Petroleum Institute has promulgated a series of standards for the oil and gas industry, including standards for welded pipes and seamless pipes, such as API 5L.
(3) DIN standards: The German Standardization Organization has promulgated a number of steel pipeline standards, such as DIN 2458, DIN 1626, etc.
(4) GB standards: The China National Standardization Administration Committee has promulgated a series of national standards for welded pipes, such as GB/T 3091, GB/T 9711, etc.
These standards cover the material, size, manufacturing process, inspection requirements, etc. of welded pipes, ensuring the quality and safety of welded pipe products. In actual procurement and use, standard products that meet the requirements should be selected based on specific project needs and relevant national/regional regulations and standards.
4. Classification and uses of large diameter welded pipes
1) Classification
According to the welding method, it is divided into two types: straight seam welding and spiral welding.
According to the purpose, they are divided into structural steel pipes, steel pipes for fluid transportation and standard mechanical steel pipes.
2) Uses
Structural steel pipes: used in load-bearing members, supporting members and steel structures in some engineering projects.
Steel pipes for fluid transportation: used to transport fluids and gases, such as water supply pipelines, oil pipelines, and natural gas pipelines.
Standard mechanical steel pipe: used in the manufacture of mechanical equipment and parts.
In addition, in the mining and power industries, large-diameter welded pipes are also used to transport ore and power lines.
5. Advantages and disadvantages of large diameter welded pipe
Advantage:
1. The weld seam has high strength and can withstand greater pressure.
2. Good corrosion resistance, can be used for a long time without being damaged by corrosion.
3. Good plasticity and processability, can be cut and processed according to engineering needs.
4. The overall performance is stable and reliable.
Disadvantages :
1. Cracks are prone to occur during welding.
2. Hydraulic testing and flaw detection are difficult.
3. The inner wall of the pipeline has concentrated stress and local shrinkage, making it difficult to withstand external loads.
6. Manufacturing process of large diameter welded pipe
(2) Spiral welded pipe (SSAW steel pipe): This process is to roll the steel plate into a tube shape through a plate rolling machine, and then weld it through a continuous spiral welding process. Spiral welded pipes are suitable for pipes with larger diameters and thicker walls, and are mainly used to transport oil, natural gas or other media.
(4) Cold drawing method: After heating the steel billet to an appropriate temperature, the welded pipe is made by cold drawing process. This process is suitable for producing welded pipes with thin wall thickness and high dimensional accuracy requirements.
Go here to learn more about " Welded Pipe HS Code"