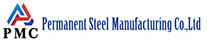
In the modern industrial field, ERW pipe, as a key piping material, plays an irreplaceable and important role. ERW, or Electric Resistance Welding, is a tubular product that is made by heating the edge of a steel strip to its melting point and fusing it under pressure through resistance welding to form a longitudinal weld.
Although ERW steel pipes have certain performance advantages, in complex and changing use environments, the material properties of the steel pipes themselves are often difficult to meet the needs of long-term stable operation. At this time, the coating is like a layer of solid protective armor for the steel pipe, which becomes a key factor in ensuring its performance and life. The following article will introduce the ERW steel pipe coating in detail.
Why does ERW pipe need coating?
ERW pipes are manufactured using high-frequency resistance welding technology and have the advantages of high production efficiency and low cost. They are widely used in urban water supply, gas transmission, industrial fluid pipelines and other fields. However, when exposed to complex environments, bare metal pipes are extremely vulnerable to corrosion and wear, leading to leakage, shortened life and other problems. At this time, high-performance coatings become the key line of defense to protect pipelines.
Key Benefits of ERW Pipe Coatings
1. Excellent anti-corrosion ability
Adopting advanced epoxy coating, polyethylene (PE) coating and other technologies, it can effectively isolate the erosion of oxygen, moisture and chemical media, and provide long-term protection for pipelines even in wet soil, marine environment or chemical corrosion areas. According to authoritative testing, the service life of ERW pipes treated with high-quality coatings can be extended by 3-5 times.
2. High-strength wear protection
For working conditions with severe wear, such as the transportation of fluids containing solid particles, our ceramic composite coating or polyurethane coating can significantly improve the wear resistance of the inner wall of the pipeline, reduce the wall thickness reduction caused by friction, and ensure the long-term safe operation of the pipeline.
3. Flexibility to adapt to extreme environments
Whether in extremely cold areas of -40℃ or high temperatures of +200℃, our special coatings can maintain stable performance. For example, high-temperature resistant silicone coatings can be used for steam pipes, while cold-resistant modified epoxy coatings are suitable for gas pipelines in cold northern regions.
4. Environmental protection and safety are equally important
All coating materials comply with national environmental protection standards, are non-toxic and harmless, and are especially suitable for drinking water, food processing and other fields with strict hygiene requirements. At the same time, the coating surface is smooth, which can reduce fluid transportation resistance and save energy consumption.
Common coating types and characteristics
1. Epoxy coating
Cured by epoxy resin, it has strong adhesion and excellent chemical resistance, especially water and soil corrosion resistance.
It is divided into liquid epoxy (cured at room temperature, suitable for small and medium diameters) and powder epoxy (cured at high temperature, uniform coverage, suitable for large diameters).
Application: urban water supply and drainage, gas transmission pipelines, and industrial wastewater treatment pipelines.
2. Polyethylene (PE) coating
Including ordinary PE and three-layer PE (bottom layer epoxy + middle layer adhesive + outer layer PE), impact resistance, wear resistance, good flexibility, suitable for buried pipelines.
Due to its composite structure, the three-layer PE coating has both the anti-corrosion properties of epoxy and the mechanical protection capabilities of PE, and is widely used in long-distance oil and gas transmission branches.
3. Zinc coating (galvanizing)
It is formed by hot-dip galvanizing or electro-galvanizing, and uses the sacrificial anode effect of zinc to protect the steel pipe, which is low-cost.
It is suitable for dry or slightly corrosive environments, such as low-pressure water supply and pipes for building structures, but its salt spray resistance is not as good as epoxy or PE.
4. Other special coatings
Food-grade coatings: such as polytetrafluoroethylene (PTFE), which is used for fluid transportation in the food and pharmaceutical industries to meet hygiene requirements.
High-temperature resistant coatings: such as ceramic or silicon-based coatings, which are suitable for industrial pipelines with higher temperatures (100-200°C).
Key points of coating process
1. Pretreatment: Before coating, the surface oxide scale and oil stains of the steel pipe need to be removed by pickling, sandblasting, etc. to ensure the adhesion of the coating.
2. Quality control: Coating thickness (usually 50-300μm, adjusted according to type), uniformity and pinhole detection are key and must comply with industry standards (such as GB/T 23257 "Polyethylene Anticorrosion Layer for Buried Steel Pipelines").
Choose the right coating to get the most out of ERW pipe
Urban water supply system: Food-grade epoxy coating is used to ensure water safety and meet the GB/T 17219 hygiene standard.
Gas transmission pipeline: Three-layer PE composite coating, combined with epoxy primer, adhesive and polyethylene outer layer, provides triple protection, suitable for long-distance, high-pressure transmission.
Chemical industry: Acid and alkali resistant fluorocarbon coating or phenolic resin coating can resist erosion by various highly corrosive media.
Marine engineering: Zinc-aluminum alloy coating + epoxy resin sealing layer, double protection against seawater scouring and salt spray corrosion.
Read more: ERW Pipe, DOM Pipe, Seamless Pipe, What are the Differences?