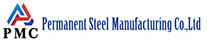
Selecting the appropriate steel pipe for pipeline transportation is essential for ensuring operational safety, long-term durability, and cost-effectiveness. Whether the pipeline carries oil, gas, water, or other fluids, the right choice depends on a careful assessment of material properties, compliance with industry standards, and the specific environmental conditions of the application. This passgae highlights the critical factors to consider when making your selection.
Understand the application requirements
In such cases, seamless steel pipes or LSAW (Longitudinal Submerged Arc Welded) pipes are often preferred due to their enhanced performance and reliability in demanding environments. Proper matching of pipe specifications with operational needs helps prevent failures, minimize maintenance, and ensure safe, long-term service.
Choose the right steel grade and standard
Ensure the pipe meets relevant international standards, such as:
API 5L for oil and gas pipelines
ASTM A106 for high-temperature service
EN 10208 / ISO 3183 for line pipe applications
Selecting the correct steel grade (e.g., X42, X52, X70) ensures the pipe can withstand mechanical stress and corrosive environments.
Evaluate pipe type: seamless vs welded
When selecting steel pipes for pipeline transportation, it’s important to understand the differences between seamless and welded pipe types, as each offers distinct advantages depending on the application.
Seamless pipes: Manufactured without any welds, seamless pipes provide exceptional strength, uniformity, and pressure resistance. They are ideal for high-pressure systems, harsh environments, and long-distance pipelines where structural integrity is critical and failure risk must be minimized.
ERW (Electric Resistance Welded) Pipes: These pipes are produced by welding the seam using high-frequency electrical current. ERW pipes are cost-effective and suitable for transporting fluids under moderate pressure. They are commonly used in urban distribution systems, structural applications, and short-to-medium-distance pipelines.
LSAW (Longitudinal Submerged Arc Welded) / SSAW (Spiral Submerged Arc Welded) Pipes: Designed for large-diameter and high-capacity pipelines, these welded pipes are commonly used in cross-country oil and gas transmission. LSAW pipes offer high dimensional accuracy and weld strength, while SSAW pipes are more economical for long runs with lower pressure requirements.
Consider Corrosion Resistance
Pipes used in corrosive or marine environments should feature internal and external anti-corrosion coatings, such as:
3LPE/3LPP coatings
Fusion bonded epoxy (FBE)
Concrete coatings for underwater or trench installations
Proper corrosion protection significantly extends the pipeline’s service life.
Assess quality certification and testing
Always request a Material Test Certificate (MTC) and verify the results of non-destructive tests such as ultrasonic testing, eddy current testing, or hydrostatic pressure testing. Pipes should comply with ISO, API, or ASME quality systems for guaranteed performance.
Cost balance principle
On the premise of ensuring safety, the cost-effective solution is preferred:
Large diameter (DN800 and above), low pressure scenario: spiral seam welded steel pipe (cost is 30%-50% lower than seamless pipe);
Small diameter, high pressure scenario: seamless steel pipe (weld strength of welded pipe is difficult to meet);
Low corrosive media: ordinary carbon steel + anti-corrosion coating (cost is more than 60% lower than stainless steel).
Conclusion
Choosing the right steel pipe for pipeline transportation depends on a combination of technical requirements, industry standards, and environmental conditions. By focusing on pipe type, material grade, corrosion protection, and certification, you can ensure safe and long-lasting pipeline performance.
Read more: How does Pipeline Transport Work?