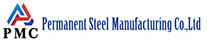
Spiral submerged arc welded pipe (SSAW) is a strip steel coiled pipe whose advancing direction has a forming angle (adjustable) with the center line of the forming pipe. It is welded while forming, and its weld is spiral. The advantage is that the same specification of strip steel can be produced steel pipes of various diameters have a large range of raw materials. The welding seam can avoid the principal stress and the stress is better. The disadvantage is that the geometrical size is poor. The length of the weld welding defects such as slag inclusion and welding deviation, the welding stress is in the state of tensile stress. The general design code for long-distance oil and gas pipelines stipulates that spiral submerged arc welded pipes can only be used in Category 3 and Category 4 areas. In foreign countries, this process is improved and the raw material is changed to steel plate to separate the forming and welding. After pre-welding and precision, and cold expansion after welding, the welding quality is close to U0E pipe. At present, there is no such process in China. It is a spiral pipe in my country. The spiral steel pipe used in the "West-East Gas Pipeline" is still produced according to the traditional technology, but the pipe end has been expanded in diameter. The United States, Japan and Germany generally reject submerged arc welding and believe that submerged arc welding is not suitable for the main line; Canada and Italy use submerged arc welding in some parts, and Russia uses submerged arc welding in a small amount, and they have formulated very strict supplementary conditions. Due to historical reasons , Most domestic trunk lines still use submerged arc welding.
B) ERW does not form a welding pool, so the welding dross ability is poor. If there is slag inclusion on the edge of the raw material, it can only remain in the weld and become a quality risk. Since submerged arc welding forms a welding pool, it is beneficial for slag inclusions to float in the slag.
C) There is no slag/gas protection during ERW welding (submerged arc welding has slag protection formed by flux), and the welded joint structure at high temperature is easily oxidized, which makes the welded joint have a tendency to embrittlement.
D) ERW has the characteristics of high local heating temperature and short cooling time. The welding temperature field has a large gradient, which is prone to hardening phase and large welding stress. The plasticity and toughness of the welded joint are not ideal. Therefore, all ERW steel pipes in the country require post-weld heat treatment (Q+T or Q+N), but domestic the post-weld heat treatment process is not yet mature.
F) Since ERW is welded by pressing molten metal, it is difficult to use NDT for effective inspection. Therefore, incomplete fusion and gray spots are the problems of ERW steel pipes, which have been difficult to effectively solve for decades. The ditch corrosion in ERW pipeline failure is mainly caused by unfusion. (Refer to Welded Pipe "Oil and Gas Transmission Pipeline Failure Accidents and Typical Cases")
G) ERW will inevitably form more T-joints during pipeline construction, while submerged arc welding will not. As we all know, the T-joint is the place where the stress is the most concentrated, which reduces the fatigue life of the welded joint.
Tips: ASTM A53 covers seamless and welded steel pipe with nominal wall thickness. The surface condition is usually black and hot-dipped galvanized. ASTM A53 is produced mainly for pressure and mechanical applications, and is also used for transport of steam, water, gas line pipes.
ASTM A53 Grade B is the material under the American steel pipe standard, API 5L Gr.B is also the American standard material, A53 GR.B ERW refers to the electric resistance welded steel pipe of A53 GR.B; API 5L GR.B Welded refers to the material Welded steel pipe of API 5L GR.B.