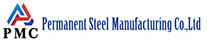
Stainless steel pipe is a hollow long round steel, which is widely used in industrial pipelines such as petroleum, chemical, medical, food, light industry, mechanical instruments, and mechanical structural parts. 304 stainless steel pipe is a grade of stainless steel produced according to the American ASTM standard. 304 stainless steel pipe is equivalent to my country's 0Cr19Ni9 (0Cr18Ni9) stainless steel pipe. 304 contains 19% chromium and 9% nickel. German standard: DIN2462
304 stainless steel pipes can be used as pipelines transportation of liquids and gases, and can be used to transport fluids, liquids, semi-fluids, etc. in production and the fields of industrial food processing, etc. As a conveying pipeline, the transported materials will generate pressure on the inner wall of the 304 stainless steel pipe. Therefore, in industrial production, the quality requirements for the stainless steel pipe welds are relatively high. Manufacturers will conduct non-destructive testing on the stainless steel pipes before leaving the factory to ensure the sealing of the welds. Non-destructive testing of 304 stainless steel welds is not only to ensure the service life of the system equipment, but also to prevent the occurrence of production accidents.
Common defects in 304 stainless steel pipe welds
a) weld bead b) crack c) slag inclusion d) pore e) undercut f) incomplete penetration
(1) Overlap. The welding rod melts too fast, the arc is too long, the current is too large, the welding speed is too slow, and the welding rod is improperly moved.
(2) Slag inclusion. The molten pool is not stirred during welding, the weldment is not clean, the current is too small, and the slag is not completely removed during layered welding.
(3) Cracks: Unreasonable welding structure design, improper welding process, too fast cooling of the weld, and high carbon, sulfur, and phosphorus content in the weldment.
(4) Gas pores. The weld is unclean, the electrode is wet, the arc is too long, the welding speed is too fast, the current is too high, and the carbon content in the weld is high.
(5) Undercut. The current is too high, the electrode is improperly moved, the arc is too long, and the electrode angle is incorrect.
(6) Incomplete penetration. The current is too high, the welding speed is too fast, the weld is unclean, the electrode is not aligned with the weld, and the groove is too small.
Five methods for nondestructive testing of 304 stainless steel pipe welds
(1) Ultrasonic flaw detection (UT) is a non-destructive flaw detection method that uses an ultrasonic flaw detector to detect internal defects in welds. This method is suitable for thick plates and can identify defects within 5 mm. The defect detection cycle is short, the wood formation is low, the equipment is simple, and it is harmless to the operator, but it cannot accurately determine the nature of the defect.
(2) Eddy current testing (ET) Eddy current testing is based on the principle of electromagnetic induction. When a steel pipe (referring to carbon steel, alloy steel and stainless steel) passes through an alternating current winding, a skin effect occurs on the surface or near the surface of the steel pipe, causing the eddy current at the defective part to change, resulting in a change in the impedance or induced voltage of the winding, thereby obtaining a signal about the defect. Defects can be identified from the amplitude and phase of the signal. Discontinuous defects on the inner and outer surfaces of the steel pipe, such as cracks, incomplete penetration, slag inclusions, pores, pitting, etc., can be effectively identified and are sensitive to open linear defects.
(3) Penetrant testing (PT) is a non-destructive testing method that uses the penetration of penetrants with fluorescent dyes (fluorescence method) or red dyes (coloring method) to display tiny defects on the surface of welded joints. During the inspection, the surface to be tested should be smooth and clean. This method is divided into fluorescent testing and coloring testing. The measurement accuracy of fluorescent testing is higher, up to 10um. Coloring testing is a commonly used method for surface inspection of welded parts.
(4) Radiographic testing (RT) is a non-destructive inspection method that uses X-rays or v-rays to irradiate welded joints to check for internal defects. It can accurately display the basic situation of the type, shape, size, location and distribution of welding technical defects in different welds. The evaluation standards are based on the "Radiography Method and Quality Classification of Steel Fusion Welded Butt Joints" (GB3329-87). The long-term operation of the defect detection method has a certain impact on the operator's health.
(5) Magnetic particle testing (MT) is a non-destructive testing method that uses the phenomenon that the leakage magnetic field generated by the surface defects of ferromagnetic materials in a strong magnetic field absorbs magnetic powder. At the defect, due to the leakage magnetic field, the scattered iron powder will be absorbed in a concentrated manner. The location and size of the welding technical defects can be determined based on the shape, thickness and amount of the adsorbed iron oxide powder. This method is not suitable for non-magnetic austenitic stainless steel.
Read more: Acceptance Criteria for 304 Stainless steel pipes