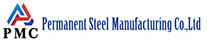
Seamless steel pipes
Seamless steel pipes are perforated from whole round steel, and steel pipes without welds on the surface are called seamless steel pipes. According to the production method, seamless steel pipes can be divided into hot-rolled seamless steel pipes, cold-rolled seamless steel pipes, cold-drawn seamless steel pipes, extruded seamless steel pipes, and top pipes. According to the cross-sectional shape, seamless steel pipes are divided into two types: round and special-shaped. Special-shaped pipes include square, oval, triangular, hexagonal, melon seed, star, and finned pipes.
The maximum diameter is 900mm and the minimum diameter is 4mm. Seamless steel pipes are mainly used as petroleum geological drilling pipes, cracking pipes for petrochemical industry, boiler pipes, bearing pipes, and high-precision structural steel pipes for automobiles, tractors, and aviation.
Can seamless steel pipes be grooved?
Seamless steel pipe (ASTM A106) can be processed and modified, such as cutting, drilling, chamfering, welding, etc., but can it be grooved? The answer is yes. Seamless steel pipe can be grooved, cutting grooves of different shapes on the surface of the pipe to increase the internal surface area and resistance of the pipe and improve the fluid delivery efficiency. The main groove processing methods include cutting, rolling, die opening, etc.
The following are commonly used seamless steel pipe groove methods
1. Cutting method: Use machine tools or cutting tools to cut the pipe surface into the required groove shape. This method is suitable for occasions with complex groove shapes, irregular sizes, or high precision requirements.
2. Rolling method: Use steel balls, steel wheels and other rolling tools to process the surface of the pipe and roll out grooves on the surface. This method is suitable for occasions where the groove shape is relatively simple, the size is regular, or the precision requirement is not high.
3. Moulding method: Use a mould to press the pipe surface into the required groove shape. This method is suitable for large-scale production of pipes of the same specification, such as floor heating pipes.
The influence of seamless steel pipe grooves
1. Structural Integrity:
Stress Concentration: Grooves can act as points of stress concentration, where the pipe may be more susceptible to fatigue, cracking, or failure under high pressure or cyclic loading. This is especially important in high-pressure applications, as grooves can weaken the pipe if not done correctly.
Reduced Wall Thickness: Grooving reduces the effective wall thickness in the grooved area, which can decrease the pipe's overall strength and its ability to handle internal pressures.
2. Pressure Capacity:
Lowered Pressure Rating: Grooves can reduce the pressure rating of the pipe because they diminish the pipe's ability to withstand internal forces. For pipes that operate under high-pressure conditions, it's crucial to calculate the reduced pressure capacity after grooving.
3. Flow Dynamics:
Turbulence: Depending on the groove's depth and location, the internal flow of fluid or gas could be affected. Grooves that are too deep or improperly aligned might cause turbulence, leading to efficiency losses or increased wear inside the pipe.
Flow Restriction: Grooves on the inside of the pipe (e.g., for threaded connections) can potentially restrict flow, leading to pressure drops or reduced flow rates.
4. Corrosion Potential:
Increased Corrosion Risk: Grooves can become sites where corrosion initiates, especially if the grooving process leaves the metal surface rough or if the pipe is used in a corrosive environment. Proper surface treatment or protective coatings may be needed to mitigate this risk.
5. Impact on Joint Connections:
Joint Integrity: Grooved pipes are often used in mechanical joints or coupling systems. If the grooves are not properly made, the joint may not be as secure, leading to leaks or joint failure under load.
6. Installation and Maintenance:
Simplified Assembly: On the positive side, grooved pipes are easier and faster to assemble, disassemble, and adjust compared to welded or threaded connections. This can reduce installation time and maintenance costs.
Alignment: Proper alignment during the grooving process is essential to ensure a secure fit with couplings and other components. Misaligned grooves can lead to improper fitting and potential leaks.
7. Impact on Mechanical Properties:
Changes in Mechanical Properties: The mechanical properties of the pipe, such as tensile strength and toughness, might be affected by the grooving process, especially if the process involves significant deformation or heating of the pipe material.