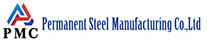
Steel pipes are an indispensable and important material in many fields such as construction and machinery manufacturing. When it comes to European standard steel pipes, EN 10210 and EN 10219 are often mentioned. They play a key role in regulating the production and quality control of steel pipes. EN 10219 and EN 10210 are two of the most commonly used standards in manufacturing welded and seamless steel tubes for various applications, including infrastructure and green energy sectors.
Overview: EN 10210 vs EN 10219
EN 10210: This standard covers hot-formed (extruded), seamless steel tubes.
It mainly targets steel pipes produced through hot rolling process, focusing on standardizing technical requirements in terms of material, mechanical properties, surface quality, etc., to ensure that the material has high strength and resistance to plastic deformation.
EN 10219: This standard applies to cold-formed welded steel tubes. It is mainly applicable to structural hollow sections made by welding thin steel sheets at ambient temperature. Focus on the quality control of the welding process after cold forming, as well as the performance of the finished product in actual use, especially in special environments such as low temperature resistance.
Manufacturing Process: EN 10210 vs EN 10219
The hot rolling process of EN 10210 is to heat the steel billet to a high temperature, making it in an austenitic state, and then rolling it through a rolling mill. In this process, the high temperature enhances the plasticity of the steel billet, making it easier to be processed into various shapes. It can also eliminate the stress inside the steel billet, refine the grains, and improve the comprehensive mechanical properties of the material. For example, the hot-rolled steel pipes used in large-scale building steel beams use this process to obtain good strength and toughness.
The cold forming welding process of EN 10219 is to cold bend the steel strip at room temperature to achieve the required shape, and then connect the interface by welding. During the welding process, it is necessary to strictly control the welding parameters, such as current, voltage, welding speed, etc., to ensure the quality of the weld and prevent defects such as cracks and pores. For example, when manufacturing welded steel pipes for small mechanical frames, it is necessary to accurately control the cold forming and welding links to ensure product quality.
Size and wall thickness: EN 10210 vs EN 10219
EN 10210: Hot-rolled steel tubes under the EN 10210 standard have a variety of common outer diameter specifications. For example, 114.3mm and 168.3mm are commonly used in building steel structures. The wall thickness range is usually around 3mm - 20mm, which can meet the different strength and stability requirements of large building structures.
EN 10219: Cold-formed welded steel pipes according to EN 10219 standard have a wide range of specifications for outer diameter and wall thickness. In the manufacture of some small equipment, steel pipes with smaller outer diameters, such as 40mm, 50mm, etc., and wall thicknesses generally between 1.5mm and 8mm, may be used, with more emphasis on processing accuracy and performance stability at smaller sizes.
Steel Grades and Material Properties: EN 10210 vs EN 10219
EN 10210: The hot-formed tubes under this standard can include higher-grade materials such as S355J2H, S420, and S460. These grades offer improved mechanical properties, such as better fatigue resistance and enhanced strength, making them ideal for heavy-duty applications.
EN 10219: The standard covers mild steel grades like S235, S275, and S355, which are commonly used for general construction purposes. These grades are designed for good weldability, moderate strength, and ease of fabrication.
Performance: EN 10210 vs EN 10219
EN 10210: From the perspective of mechanical properties, the hot-rolled steel tubes of EN 10210 standard have good strength and toughness due to the high temperature during the hot rolling process that causes the grains to fully recrystallize and the structure to be uniform.
EN 10219: Cold-formed welded steel pipes according to EN 10219 standard have work hardening during cold working, so their yield strength will be improved, but their toughness may be slightly lower than that of hot-rolled steel pipes.
Applications: EN 10210 vs EN 10219
EN 10210: With enhanced strength and performance, hot-formed tubes are well-suited for demanding applications, including:
1. Heavy-duty construction projects like high-rise buildings, bridges, and industrial facilities
2. Offshore and marine engineering structures
3. Equipment and structures in energy production, such as oil rigs and power plants
4. Renewable energy systems, including geothermal and hydroelectric installations
EN 10219: These tubes are commonly utilized in applications where cost-effectiveness and moderate performance are key. Typical uses include:
1. Structural frameworks and scaffolding in building construction
2. Support structures in green energy systems, such as wind turbine towers and solar panel frames
3. Light structural supports in bridges and transportation projects
Cost Comparison: EN 10210 vs EN 10219
EN 10210: Hot-formed tubes tend to be more costly due to the energy-intensive manufacturing process and additional processing steps. Nevertheless, they offer greater value over time in applications that demand superior strength and durability.
EN 10219: Cold-formed tubes are typically more affordable thanks to a faster and less complex production process. They are ideal for cost-sensitive projects where high performance is not a primary concern.
EN 10210 vs EN 10219 : How to Choose the Right Option
Choose EN 10219 if your project prioritizes cost efficiency and moderate structural demands. Cold-formed tubes under this standard are ideal when:
You're working with a limited budget and need an economical solution.
The application involves light to moderate load-bearing, such as in secondary structural elements, frameworks, or scaffolding.
Fast lead times and ease of fabrication are important.
A balance between performance and price is acceptable for non-critical structures.
Choose EN 10210 when your project requires superior mechanical properties and long-term reliability. Hot-formed tubes under this standard are recommended for:
High-strength applications where structural integrity is crucial, such as in heavy construction, bridges, or industrial infrastructure.
Projects exposed to harsh or fluctuating environmental conditions, requiring excellent fatigue and impact resistance.
Demanding sectors like offshore, energy production, or transportation, where failure is not an option.
Applications needing thick-walled or seamless structural sections that can withstand extreme loads and stress.
In summary, EN 10219 is best for standard construction needs with moderate requirements, while EN 10210 is the go-to choice for high-performance applications where safety, strength, and durability are non-negotiable.