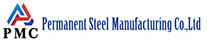
The quality inspection of elbow fittings is a key link to ensure their safe and reliable operation in the oil and gas industry. The inspection methods cover appearance, size, material, performance and non-destructive testing, as follows:
Appearance inspection of elbow fittings
1. Visual inspection
Surface quality: Check whether the elbow surface is smooth, and whether there are defects such as cracks, sand holes, pores, folds, and heavy skin.
Coating integrity: If the elbow has an anti-corrosion coating (such as epoxy powder, 3PE coating), check whether the coating is uniform, without falling off or damage.
Marking clarity: Confirm whether the specifications, models, materials, pressure levels and other markings on the elbow are clear and legible.
2. Penetrant testing (PT)
Applicable to detecting surface opening defects (such as tiny cracks). Through spraying penetrant, cleaning, imaging and other steps, the defect will show red marks for easy positioning.
Dimensional inspection of elbow fittings
1. Geometric dimension measurement
Curvature radius: Use a special caliper or a three-dimensional measuring machine to check whether the bending radius of the elbow meets the design requirements (such as long radius elbow R=1.5DN, short radius elbow R=1.0DN).
Wall thickness uniformity: Use an ultrasonic thickness gauge or caliper to measure the wall thickness of different parts of the elbow to ensure that the wall thickness deviation is within the allowable range (usually ≤12.5% of the nominal wall thickness).
Angle deviation: Use a protractor or a special mold to detect the bending angle of the elbow (such as 90° elbow, 45° elbow) to ensure that the angle error meets the standard (such as ±1°).
End verticality: Check the verticality of the two end faces of the elbow to the axis to avoid deflection during installation.
2. Ovality detection
Use an internal micrometer or external caliper to measure the maximum and minimum outer diameters of the elbow bending section, calculate the ovality (= (maximum outer diameter - minimum outer diameter) / nominal outer diameter × 100%), and ensure that it is ≤8% (DN≤300) or ≤5% (DN>300).
Material testing of elbow fittings
1. Chemical composition analysis
Spectral analysis: Use a direct reading spectrometer or a handheld X-ray fluorescence spectrometer to quickly detect the content of elements such as C, Si, Mn, S, and P in the elbow material to confirm whether it meets the standards (such as ASTM A234, GB/T 12459, etc.).
Carbon and sulfur analysis: For elbows with high precision requirements, a high-frequency infrared carbon and sulfur analyzer is used to determine the precise content of carbon and sulfur.
2. Mechanical properties test
Tensile test: Take samples from the elbow and test the tensile strength (Rm), yield strength (ReH) and elongation after fracture (A) on a tensile testing machine to ensure compliance with standard requirements (such as API 5L, GB/T 9711).
Impact test: Perform a Charpy V-notch impact test on the elbow at low or normal temperature to measure the impact energy (KV2) and verify whether its toughness meets the use conditions (such as deep sea or polar environment).
Hardness test: Use a Brinell hardness tester or Rockwell hardness tester to test the hardness of the elbow surface to ensure that the hardness value is within the specified range (such as 180-220HB).
Non-destructive testing (NDT) of elbow fittings
Ultrasonic testing (UT)
Applicable to detecting internal defects of elbows (such as interlayers, pores, cracks). The ultrasonic probe emits sound waves, and the defect location and size are determined based on the reflected signal, with high detection sensitivity.
Radiographic testing (RT)
Perform X-ray or gamma ray transillumination on the elbow and observe internal defects through film or digital imaging system. It is suitable for detecting volume defects (such as pores and slag inclusions), but the detection cost is relatively high.
Magnetic Particle Testing (MT)
Applicable to surface and near-surface defect detection of ferromagnetic material elbows. By magnetizing the elbow and sprinkling magnetic powder, magnetic traces will be formed at the defects, making them easy to identify.
Eddy current testing (ET)
Used to detect cracks, corrosion and other defects on the elbow surface or near the surface. The eddy current sensor is used to scan the elbow surface and judge the defect according to the impedance change. It is suitable for batch testing.
Pressure and sealing test of elbow fittings
Water pressure test
Fill the elbow with water, remove the air and pressurize it to 1.5 times (or higher) the design pressure, keep it for a certain period of time (such as 5 minutes), and observe whether the elbow has leakage or deformation. It is suitable for verifying the overall strength and sealing of the elbow.
Air pressure test
For elbows that are not suitable for water pressure test (such as those with high internal drying requirements), air pressure test can be used. The pressure is usually 1.15 times the design pressure, but safety measures must be strictly controlled.
Helium mass spectrometer leak detection
For elbows with high sealing requirements (such as high-pressure natural gas pipelines), a helium mass spectrometer leak detector is used to detect tiny leaks with a sensitivity of up to 10⁻⁹ Pa·m³/s.
Special environment adaptability test
Low temperature toughness test
For elbows used in polar or deep sea environments, low temperature impact tests (such as -46°C or lower) are carried out to ensure that the material still maintains good toughness at low temperatures and avoids brittle fracture.
Hydrogen sulfide corrosion resistance test (HIC/SSC)
Hydrogen induced cracking (HIC) and sulfide stress corrosion cracking (SSC) tests are carried out on elbows used in sulfur-containing oil and gas fields to verify their anti-sulfur corrosion performance.
Corrosion resistance test
Through salt spray test, cyclic corrosion test, etc., the corrosion resistance of elbow coating or material is evaluated to ensure its service life in harsh environment.
Read more: Are Elbow Fittings Safe in High Pressure Environments?