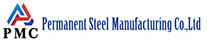
Non-destructive testing (NDT) is crucial to ensuring the quality of non-standard smls pipes(seamless steel pipe), even more important than for standard seamless steel pipes. This is because the particularity of non-standard steel pipes determines that their quality control faces greater challenges.
Quality risks of non-standard smls steel pipes
Large dimensional deviation: Since it is non-standard customization, the dimensional tolerance may be larger than that of standard steel pipes, and it is more likely to have dimensional deviation problems, affecting subsequent processing and use.
Special materials: The use of special materials or composition adjustments may make process control during smelting and rolling more difficult and more prone to internal defects.
High performance requirements: Non-standard steel pipes are often used in special working conditions and have higher performance requirements. Any potential defects may lead to serious safety accidents.
Insufficient production experience: Manufacturers may have relatively insufficient experience in producing non-standard steel pipes, making quality problems more likely to occur.
The role of non-destructive testing in quality assurance of non-standard smls pipes
Nondestructive testing can detect internal and surface defects of steel pipes without damaging them, thereby effectively controlling the quality of non-standard steel pipes. Its main functions include:
Detecting internal defects: Ultrasonic testing (UT) and radiographic testing (RT) can effectively detect cracks, pores, inclusions, uneven wall thickness and other defects inside steel pipes. These defects cannot be seen by the naked eye, but may seriously affect the mechanical properties and service life of the steel pipe.
Detection of surface defects: Eddy current testing (ET), magnetic particle testing (MT), penetrant testing (PT) and other methods can effectively detect cracks, scratches, oxide scale and other defects on the surface of steel pipes, which will affect the corrosion resistance and appearance quality of the steel pipes.
Accurately measure wall thickness: Methods such as ultrasonic thickness measurement can accurately measure the wall thickness of steel pipes to ensure that it meets the drawing or contract requirements.
Provide comprehensive quality assessment: Through the comprehensive application of multiple non-destructive testing methods, the internal and surface quality of non-standard steel pipes can be comprehensively evaluated, thereby effectively controlling product quality.
Commonly used nondestructive testing methods and their applicability
Ultrasonic flaw testing (UT): It is suitable for testing steel pipes of various materials. It is sensitive to defects such as internal cracks and inclusions. It has high detection efficiency and relatively low cost. It is one of the most widely used methods.
Radiographic testing (RT): Suitable for testing steel pipes with thicker walls. It can visually display the shape and size of defects, but it is more expensive and poses radiation hazards.
Eddy current testing (ET): Suitable for detecting surface and near-surface defects of steel pipes. It has fast detection speed and high degree of automation, but its detection ability for deep defects is limited.
Magnetic particle testing (MT): It is suitable for detecting surface and near-surface defects of steel pipes containing magnetic materials. It is simple to operate and has low cost, but it can only detect magnetic materials.
Penetrant testing (PT): Suitable for detecting open defects on the surface of steel pipes of various materials. It is simple to operate and low-cost, but it can only detect surface defects.
According to the specific material, size, performance requirements and operating conditions of non-standard steel pipes, appropriate non-destructive testing methods can be selected or multiple methods can be used in combination.
The importance of nondestructive testing for non-standard smls pipes
1. Reduce safety risks: Discovering potential defects through non-destructive testing can effectively reduce the risk of safety accidents such as breakage and leakage of steel pipes during use.
2. Improve product reliability: Non-destructive testing can ensure that the quality of non-standard steel pipes meets the requirements and improve product reliability and service life.
3. Reduce economic losses: By conducting non-destructive testing during the production process, defective products can be discovered and eliminated in a timely manner, reducing rework and scrap losses caused by quality problems.
4. Meeting special application requirements: Some special application fields, such as aerospace, nuclear power, etc., have extremely high quality requirements for steel pipes and must undergo strict non-destructive testing.
Conclusion
In summary, non-destructive testing is a key link in the quality assurance of non-standard smls steel pipes. By selecting appropriate non-destructive testing methods, product defects can be effectively discovered and controlled, safety risks can be reduced, product reliability can be improved, and special application requirements can be met.
Read more: Non-standard SMLS Pipes: Special Strength of Industrial Pipes