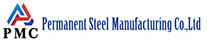
Drill Pipes
Drill pipes are a vital component of the drilling process in the oil and gas industry. They are part of the drill string, which transmits the rotary motion from the drilling rig to the drill bit and allows drilling fluids to be circulated down to the bit and back to the surface.
Oil Casing Pipes
Oil casing pipes are another crucial component in the oil and gas industry. They are used to line the wellbore after it has been drilled, providing structural integrity to the well and isolating different subsurface layers to prevent contamination between formations.
The Connection Method of Drill Pipes and Oil Casing Pipes
1. Threaded connection
The drill pipe and casing pipe are connected by specific threads, which are designed to withstand high pressure and high torque to ensure stability and safety during drilling. Common thread connection types include API threads, STC, LTC, BTC, etc. These thread types are suitable for pipes of different sizes and pressure levels to meet the needs of various drilling conditions.
2. Special buckle processing
For special application scenarios, special fastener processing may be required, such as DS55 fasteners, special fastener processing, etc., to meet specific drilling requirements. This processing can be carried out according to order requirements, ensuring a precise connection between drill pipe and oil casing.
3. Variable buckle conversion connector
During the drilling process, different sizes or types of drill pipes and casing pipes may be required depending on the drilling depth and geological conditions. Variable adapters are used to connect drill pipes and oil casing of different sizes or types to ensure the continuity and efficiency of drilling operations.
Challenges and Considerations
Torque Control: Ensuring the correct make-up torque is crucial for both drill pipe and casing pipe connections. Too little torque can lead to loose connections, while too much can damage the threads.
Inspection and Maintenance: Regular inspection of threads and connections is essential to prevent failures. This includes visual inspections, thread gauges, and non-destructive testing (NDT).
Corrosion and Wear: Both drill pipes and casing pipes are exposed to harsh environments, so their connections must be inspected regularly for signs of corrosion and wear.
Thread Protection: During transportation and storage, thread protectors are used to prevent damage to the threads, ensuring that the connections are in good condition when installed.
The connection methods for drill pipes and oil casing pipes are critical to the integrity and functionality of the well. Both types of pipes use threaded connections, but the design and application of these connections differ due to their roles in drilling and casing operations.