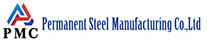
What is high frequency welding?
High-frequency welding is a new type of welding process that uses the skin effect and neighboring effect produced by high-frequency current to connect steel plates and other metal materials. The emergence and maturity of high-frequency welding technology is a key process in the production of ERW steel pipe. The quality of high-frequency welding directly affects the overall strength, quality level and production speed of welded pipe products.
The skin effect means that when an alternating current of a certain frequency passes through the same conductor, the current density is not uniformly distributed across all sections of the conductor. It will mainly concentrate on the surface of the conductor, that is, the density of the current on the surface of the conductor is high. The density inside the conductor is small, so we vividly call it: "skin effect". The skin effect is usually measured by the penetration depth of the current. The smaller the penetration depth, the more significant the skin effect. This penetration depth is proportional to the square root of the resistivity of the conductor, and inversely proportional to the square root of frequency and permeability. In layman's terms, the higher the frequency, the more current is concentrated on the surface of the steel plate; the lower the frequency, the more scattered the surface current is. It must be noted that although steel is a conductor, its magnetic permeability will decrease as the temperature rises. That is to say, when the temperature of the steel plate increases, the magnetic permeability will decrease and the skin effect will decrease.
These two effects are the basis for realizing high-frequency metal welding. High-frequency welding uses the skin effect to concentrate the energy of the high-frequency current on the surface of the workpiece; and uses the proximity effect to control the location and range of the high-frequency current flow path. The speed of the current is very fast. It can heat and melt the edges of adjacent steel plates in a short period of time, and realize butt joints through extrusion.
Tips: In case ASTM A53 Grade B in ERW (electric resistance welded) pipe, the weld seam shall be done the heat treatment with a minimum 1000°F [540°C]. In this way the no untempered martensite remains.
In case ASTM A53 B pipe in cold expanded, then expansion should not exceed 1.5% of the required OD.