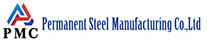
Stainless steel welded pipe, referred to as welded pipe, is a steel pipe made by welding steel or steel strip after being curled and formed by a unit and a die. The production process of welded steel pipe is simple, the production efficiency is high, the variety and specifications are many, and the equipment investment is small, but the general strength is lower than that of seamless steel pipe.
Stainless steel welded pipes are divided into straight seam welded pipes and spiral welded pipes according to the weld form. The production process of straight seam welded pipe is simple, with high production efficiency, low cost and rapid development. The strength of spiral welded pipe is generally higher than that of straight seam welded pipe. It can produce welded pipes with larger diameters using narrower billets, and can also produce welded pipes with different diameters using billets of the same width. However, compared with the straight seam pipe of the same length, the weld length increases by 30~100%, and the production speed is lower. Large diameter or thicker welded pipes are generally made directly from steel billets, while small welded pipes and thin-walled welded pipes only need to be welded directly through steel strips. Then they are simply polished and wire-drawn.
Production process of stainless steel welded pipe
1. Material Preparation:
Raw Material Selection: High-quality stainless steel coils or strips are selected as raw materials. The most common grades are 304, 316, and 321 stainless steel.
Slitting: The stainless steel coils or strips are slit into narrower widths according to the required pipe size.
2. Pipe Forming:
Uncoiling: The slit stainless steel strip is uncoiled and straightened.
Forming: The strip is passed through a series of forming rollers that gradually bend it into a cylindrical shape. The forming process can be done using various methods, such as roll forming, where the flat strip is continuously shaped into a round pipe.
3. Welding:
TIG Welding (Tungsten Inert Gas): The edges of the formed strip are welded together using TIG welding. This process is preferred for stainless steel due to its ability to create a clean, strong weld without introducing contaminants.
Laser Welding: An alternative to TIG welding, laser welding uses concentrated laser beams to weld the edges with high precision and speed.
Plasma Welding: Another method that uses plasma arc to weld the edges, suitable for thicker materials.
4. Bead Rolling:
After welding, the weld bead (the raised portion of the weld) is often rolled to reduce its height and make it flush with the pipe surface.
5. Heat Treatment (Optional):
Depending on the grade and intended use, the welded pipe may undergo heat treatment (annealing) to relieve internal stresses and improve mechanical properties. This process involves heating the pipe to a high temperature and then cooling it rapidly (quenching).
6. Sizing and Straightening:
Sizing: The pipe is passed through sizing rollers to ensure it has the correct dimensions.
Straightening: The pipe is straightened to ensure it has no bends or twists.
7. Surface Treatment:
Pickling and Passivation: The pipe is immersed in acid baths (pickling) to remove any scale or oxides from the surface, followed by passivation to form a protective oxide layer that enhances corrosion resistance.
Polishing: For applications requiring a smooth finish, the pipe may be polished to achieve the desired surface roughness.
8. Non-Destructive Testing (NDT):
The pipe undergoes various NDT methods such as ultrasonic testing, eddy current testing, or X-ray inspection to detect any defects or inconsistencies in the weld or material.
9. Cutting:
The welded pipe is cut to the desired length using saws or cutting machines.
10. Final Inspection:
The final product is inspected for dimensional accuracy, surface finish, and weld integrity. Any pipes that do not meet the required standards are rejected or reworked.
11. Packaging and Shipping:
The finished pipes are cleaned, packaged, and prepared for shipment. Protective coverings may be applied to prevent damage during transportation.
Read more: Stainless Steel Welded Pipe Processing Technology