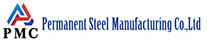
In the world of oil extraction and production, the integrity of equipment is of paramount importance. One of the key components that ensures smooth operation and safety is the oil casing. These tubular structures provide structural support and protection for the wellbore, shielding it from external pressure and environmental factors. However, one of the most persistent threats to oil casing is corrosion, which can compromise its effectiveness and lead to expensive repairs or even catastrophic failures.
Corrosion of oil casing is caused by a variety of factors, mainly exposure to corrosive elements present in the environment and fluids flowing through the casing. The harsh conditions underground, such as high temperature, pressure differentials and the chemical composition of the formation fluid, exacerbate the corrosion process. If not controlled, corrosion can weaken the casing wall, leading to leaks, casing failures and environmental hazards.
Understanding the importance of corrosion protection is essential to mitigate these risks. Effective corrosion protection can not only extend the service life of oil casing, but also improve operational efficiency and safety. To achieve this goal, the oil and gas industry has developed and implemented a number of advanced technologies and strategies.
What should be paid attention to when oil casing pipe is anti-corrosion?
1. First of all, we must do a good job in meeting water quality standards, and strictly test and manage water quality. Implement clean-up and separate injection, strengthen the cleaning of main water pipelines, ensure that the water quality in the station and bottom of the well meets the standard, and reduce the introduction of corrosion sources into the annular space;
2. For the injection wells that have been newly put into production, adopt the annulus protection liquid based on the addition of sterilization, and form a system to regularly add;3. In view of the accelerating effect of mechanical abrasion on the corrosion of the oil casing, it is recommended to add a rubber ring to the tubing coupling or a centralizer at the serious position of the well slope to avoid the tubing from scratching the casing and the process of water injection. One side contacts the bushing;
4. In view of the serious corrosion of bacteria under scale and the slow growth and killing of SRB at high temperature, high temperature water or steam at 100 degrees Celsius can be injected into the annulus regularly to kill SRB under scale;
5. It is not recommended to promote the use of cathodic protection and coated casing until the corrosion in the casing of the water injection well is not effectively controlled.
There are three main types of corrosion protection for oil casing
1. Apply anti-corrosion coating on the outer wall.
2. Apply anti-corrosion coating on the inner wall.
3. Apply anti-corrosion and cooling coating
A oil casing pipe is used in harsh oil extraction industries such as polar and ocean. It requires that the material and structure of the oil casing must have good node properties, excellent physical properties, stable chemical properties and a wide temperature adaptability range. If the oil casing pipe cannot be made, it should be coated with an anti-corrosion coating to help it cope with the harsh environment. The coating on the outer wall is used to reduce external corrosion, and the anti-corrosion coating on the inner wall is to reduce friction, reduce pipeline corrosion, and increase oil delivery.
Read more: Oil Casing Pipe Testing Method