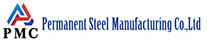
Manufacturing process of carbon steel ERW pipe:
The manufacturing process of carbon steel ERW pipe involves the following key steps:
(1) Material SelectionHigh-quality carbon steel coils or strips are selected based on the required specifications.
(2) FormingThe flat steel strip is passed through a series of rollers to gradually form it into a cylindrical shape.
(3) WeldingThe edges of the formed strip are heated to the welding temperature using a high-frequency current and then fused together under pressure to create a solid weld seam.
(4) SizingThe welded pipe is passed through additional rolls to achieve the desired dimensions and roundness.
(4) Cutting and FinishingThe pipe is cut to the required lengths, and the ends are finished according to specific customer requirements.
Common welding defects of carbon steel ERW pipes:
(1) Incomplete welding
The blunt edges in the middle (X groove) or root (V, U groove) of the parent metal joint are not completely fused together, leaving partial unfusion. Inadequate welding reduces the mechanical strength of the welded joint, and stress concentration points will be formed in the gaps and ends of the welded joint, which can easily lead to cracking when the welded parts bear load.
(2) Not fused
Between the solid metal and the filler metal (between the weld bead and the base metal), or between the filler metal (in the case of multi-pass welding, the local incomplete melting between the weld beads or between the weld layers, or during spot welding (electric resistance welding) When the base metal is not completely fused together, sometimes slag inclusions are often present.
(6) Segregation
During welding, due to the small melting area and rapid cooling of the metal, it is easy to cause uneven distribution of chemical components of the weld metal, thus forming segregation defects, mostly in the form of strips or lines and distributed along the axial direction of the weld.
(7) Undercut and burn through
Such defects are external defects of the weld. Burnthrough is the penetration (perforation) caused when the parent metal melts excessively. Excessive melting near the fusion line between the parent metal and the weld will also cause a depression in the transition zone between the deposited metal and the parent metal, which is an undercut. According to the undercut located above and below the weld, it can be divided into outer undercut (on the side with the larger opening of the groove) and inner undercut (on the bottom side of the groove). Undercut can also be said to be a groove-like defect along the edge of the weld that is lower than the surface of the base metal.
Other external weld defects:
1. Weld nodule: a local protrusion at the root of the weld. This is a metal nodule formed by the falling of liquid metal during welding. There are often incomplete penetration defects under the welding nodules, which must be paid attention to.
2. Concave or subsidence: When the root of the weld shrinks upward and is lower than the lower surface of the base metal, it is called concave. When the weld cover is lower than the upper surface of the base metal, it is called subsidence.
3. Overflow: The metal molten pool of the weld is too large, or the position of the molten pool is incorrect, causing the molten metal to overflow, and the overflowed metal fuses with the base metal.
4. Arc crater: During arc welding, the pit at the end of the weld (arc extinguishing point) or the welding rod connection (arc starting point) is lower than the surface of the weld bead base. In such pits, pores and micro-cracks are easily generated. .
5. Welding deviation: It appears as weld bead deflection or distortion on the cross section of the weld. The reinforcement height (also called weld crown and cover surface) is too high: the weld bead cover layer is much higher than the surface of the base metal. Generally, the welding process has regulations on the height of the reinforcement height. When it exceeds the specified value, the reinforcement height will be different from the parent metal The joint corners of materials can easily become stress concentration points, which is detrimental to the structural load-bearing.
The above external defects are likely to cause stress concentration points after the weldment is loaded, or reduce the effective cross-sectional area of the weld and reduce the strength of the weld. Therefore, there are generally clear regulations on the welding process, and visual inspection is often used. Inspection reveals these external defects.
Applications of carbon steel ERW pipe:
Carbon steel ERW pipes are widely used in various industrial applications, including:
(1) Oil and Gas Industry
Transportation of oil, gas, and petroleum products due to their high-pressure bearing capacity and durability.
(2) Construction
Structural applications such as building frameworks, scaffolding, and support columns.
(3) Water Transmission
Distribution and transmission systems for water and other fluids due to their corrosion resistance.
(4) Industrial Processes
Conveying various fluids and gases in industrial processing plants.
Tips: ASTM A53 is the grade of ERW high-frequency welded pipe, which is divided into Grade A and Grade B. ASTM A53 Grade B is more popular than other grades. These pipes can be bare without any coating, or they can be hot dipped or galvanized and manufactured through welding or seamless manufacturing processes. In Oil and Gas, A53 grade pipes are used in the structural and non-critical applications.