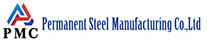
Common weld defects of welded pipes:
(1) Incomplete welding
The blunt edges in the middle (X groove) or root (V, U groove) of the parent metal joint are not completely fused together, leaving partial unfusion. Inadequate welding reduces the mechanical strength of the welded joint, and stress concentration points will be formed in the gaps and ends of the welded joint, which can easily lead to cracking when the welded parts bear load.
(2) Not fused
Between the solid metal and the filler metal (between the weld bead and the base metal), or between the filler metal (in the case of multi-pass welding, the local incomplete melting between the weld beads or between the weld layers, or during spot welding (resistance welding) When the base metal is not completely fused together, sometimes slag inclusions are often present.
The existence of cracks greatly reduces the strength of the welded joint, and the tip of the weld crack also becomes the stress concentration point after load-bearing, becoming the origin of structural fracture. Cracks may occur inside or outside the weld metal, or in the heat-affected zone of the base metal near the weld, or at the junction of the base metal and the weld, etc.
Depending on the time and temperature at which welding cracks occur, cracks can be divided into the following categories:
a. Thermal cracks (also called crystal cracks)
It occurs during the cooling and crystallization process after the weld is formed. It mainly occurs at the grain boundary. In metallography, it is called intergranular crack. Its location is mostly in the center of the weld metal and the arc crater of arc welding. It radiates longitudinally or transversely, and in severe cases can penetrate the surface and heat-affected zone. The causes of hot cracks are related to segregation during welding, uneven heating and cooling, and excessive sulfur content in the welding rod (filler metal) or base metal.
b. Cold cracks
Cracks that appear when cooled to low temperature or room temperature after welding, or cracks that appear after a period of time after welding (such cold cracks are called delayed cracks, especially alloy steels such as 14MnMoVg, 18MnMoNbg, 14MnMoNbB and other alloy steels are prone to such cracks Delayed cracking, also known as delayed cracking sensitive steel). Cold cracks mostly appear in the heat-affected zone near the fusion line of the weld bead and the base metal, and their orientation is mostly parallel to the fusion line, but there are also cold cracks that are longitudinal or transverse to the axis of the weld bead. Cold cracks are mostly transgranular cracks (cracks pass through the grain boundaries and enter the grains). The cause is that the low plasticity structure in the heat-affected zone of the weld bead cannot withstand the stress caused by the volume change and structure transformation during cooling, or the cracks in the weld seam When hydrogen atoms combine with each other to form a molecular state and enter the fine pores of the metal, it will cause a large compressive stress and the joint action of the welding stress will lead to cracking (called hydrogen embrittlement cracks), as well as the phosphorus content in the welding rod (filler metal) or base material. It is related to factors such as being too high.
c. Reheat crack
After welding is completed, if the weldment is heated again within a certain temperature range (such as heat treatment or other heating processes to eliminate welding stress, and repair welding, etc.), cracks may occur, mostly in the overheated area of the weld. , is an intergranular crack, and its cause is related to the strain caused by changes in the microstructure.
(6) Segregation
During welding, due to the small melting area and rapid cooling of the metal, it is easy to cause uneven distribution of chemical components of the weld metal, thus forming segregation defects, mostly in the form of strips or lines and distributed along the axial direction of the weld.
(7) Undercut and burn through
Such defects are external defects of the weld. Burnthrough is the penetration (perforation) caused when the parent metal melts excessively. Excessive melting near the fusion line between the parent metal and the weld will also cause a depression in the transition zone between the deposited metal and the parent metal, which is an undercut. According to the undercut located above and below the weld, it can be divided into outer undercut (on the side with the larger opening of the groove) and inner undercut (on the bottom side of the groove). Undercut can also be said to be a groove-like defect along the edge of the weld that is lower than the surface of the base metal.
Other external weld defects:
1. Weld nodule: a local protrusion at the root of the weld. This is a metal nodule formed by the falling of liquid metal during welding. There are often incomplete penetration defects under the welding nodules, which must be paid attention to.
2. Concave or subsidence: When the root of the weld shrinks upward and is lower than the lower surface of the base metal, it is called concave. When the weld cover is lower than the upper surface of the base metal, it is called subsidence.
3. Overflow: The metal molten pool of the weld is too large, or the position of the molten pool is incorrect, causing the molten metal to overflow, and the overflowed metal fuses with the base metal.
4. Arc crater: During arc welding, the pit at the end of the weld (arc extinguishing point) or the welding rod connection (arc starting point) is lower than the surface of the weld bead base. In such pits, pores and micro-cracks are easily generated. .
5. Welding deviation: It appears as weld bead deflection or distortion on the cross section of the weld. The reinforcement height (also called weld crown and cover surface) is too high: the weld bead cover layer is much higher than the surface of the base metal. Generally, the welding process has regulations on the height of the reinforcement height. When it exceeds the specified value, the reinforcement height will be different from the parent metal The joint corners of materials can easily become stress concentration points, which is detrimental to the structural load-bearing.
The above external defects are likely to cause stress concentration points after the weldment is loaded, or reduce the effective cross-sectional area of the weld and reduce the strength of the weld. Therefore, there are generally clear regulations on the welding process, and visual inspection is often used. Inspection reveals these external defects.
Read more: Analysis of Common Welding Defects of High Frequency Welded Pipe