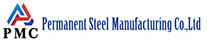
Defectos de soldadura comunes de tuberías soldadas:
(1) Soldadura incompleta
Los bordes romos en el medio (ranura en X) o en la raíz (ranura en V, U) de la unión del metal principal no están completamente fusionados, dejando una falta de fusión parcial. Una soldadura inadecuada reduce la resistencia mecánica de la unión soldada y se formarán puntos de concentración de tensiones en los espacios y extremos que no se penetran, lo que puede provocar fácilmente grietas cuando las piezas soldadas soportan carga.
(2) No fusionado
Entre el metal sólido y el metal de aportación (entre el cordón de soldadura y el metal base), o entre el metal de aportación (en el caso de soldadura de múltiples pasadas, la fusión local incompleta entre los cordones de soldadura o entre las capas de soldadura, o durante Soldadura por puntos (soldadura por resistencia) Cuando el metal base no está completamente fusionado, a veces suelen aparecer inclusiones de escoria.
La existencia de grietas reduce en gran medida la resistencia de la unión soldada, y la punta de la grieta de soldadura también se convierte en el punto de concentración de tensiones después de la carga, convirtiéndose en el origen de la fractura estructural. Pueden ocurrir grietas dentro o fuera del metal de soldadura, o en la zona afectada por el calor del metal base cerca de la soldadura, o en la unión del metal base y la soldadura, etc.
Dependiendo del tiempo y la temperatura a la que se producen las grietas por soldadura, las grietas se pueden dividir en las siguientes categorías:
a. Grietas térmicas (también llamadas grietas cristalinas)
Ocurre durante el proceso de enfriamiento y cristalización después de que se forma la soldadura. Ocurre principalmente en el límite de grano. En metalografía, se llama grieta intergranular. Su ubicación se encuentra principalmente en el centro del metal de soldadura y en el cráter del arco de la soldadura por arco. Irradia longitudinal o transversalmente y, en casos graves, puede penetrar la superficie y la zona afectada por el calor. Las causas de las grietas por calor están relacionadas con la segregación durante la soldadura, el calentamiento y enfriamiento desigual y el contenido excesivo de azufre en la varilla de soldadura (metal de aportación) o el metal base.
b. Grietas por frío
Grietas que aparecen cuando se enfrían a baja temperatura o temperatura ambiente después de la soldadura, o grietas que aparecen después de un período de tiempo después de la soldadura (tales grietas en frío se denominan grietas retardadas, especialmente los aceros aleados como 14MnMoVg, 18MnMoNbg, 14MnMoNbB y otros aceros aleados son propensos a tales grietas (craqueo retardado, también conocido como acero sensible al agrietamiento retardado). Las grietas en frío aparecen principalmente en la zona afectada por el calor cerca de la línea de fusión del cordón de soldadura y el metal base, y su orientación es mayoritariamente paralela a la línea de fusión, pero también hay grietas en frío que son longitudinales o transversales al eje de la cordón de soldadura. Las grietas en frío son en su mayoría grietas transgranulares (las grietas atraviesan los límites de los granos y entran en los granos). La causa es que la estructura de baja plasticidad en la zona afectada por el calor del cordón de soldadura no puede soportar la tensión causada por el cambio de volumen y la transformación de la estructura durante el enfriamiento. o las grietas en la costura de soldadura Cuando los átomos de hidrógeno se combinan entre sí para formar un estado molecular y entran en los poros finos del metal, provocarán una gran tensión de compresión y la acción conjunta de la tensión de soldadura provocará grietas (llamadas hidrógeno grietas por fragilidad), así como el contenido de fósforo en la varilla de soldadura (metal de aporte) o material base, que está relacionado con factores como que sea demasiado alto.
c. Recalentar la grieta
Una vez completada la soldadura, si la pieza soldada se calienta nuevamente dentro de un cierto rango de temperatura (como tratamiento térmico u otros procesos de calentamiento para eliminar la tensión de la soldadura y reparar la soldadura, etc.), pueden ocurrir grietas, principalmente en el área sobrecalentada de la soldadura., es una grieta intergranular, y su causa está relacionada con la deformación provocada por cambios en la microestructura.
(6) Segregación
Durante la soldadura, debido a la pequeña área de fusión y al rápido enfriamiento del metal, es fácil causar una distribución desigual de los componentes químicos del metal de soldadura, formando así defectos de segregación, principalmente en forma de tiras o líneas y distribuidos a lo largo del eje axial. dirección de la soldadura.
(7) Socavar y quemar
Estos defectos son defectos externos de la soldadura. El quemado es la penetración (perforación) causada cuando el metal base se funde excesivamente. La fusión excesiva cerca de la línea de fusión entre el metal base y la soldadura también causará una depresión en la zona de transición entre el metal depositado y el metal base, que es un corte socavado. Según el corte ubicado encima y debajo de la soldadura, se puede dividir en corte externo (en el lado con la abertura más grande de la ranura) y corte interno (en el lado inferior de la ranura). También se puede decir que el corte socavado es un defecto similar a una ranura a lo largo del borde de la soldadura que es más bajo que la superficie del metal base.