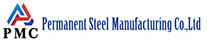
Drill pipe, as a steel pipe with threads at the tail, plays a key role in drilling operations. It is mainly used to connect the surface equipment of the drilling rig with the drilling and grinding equipment or bottom hole device at the bottom of the well. Its main function is to transport drilling mud to the drill bit, and work with the drill bit to achieve the lifting, lowering or rotating operation of the bottom hole device.
From a structural point of view, the drill pipe is made of seamless tube, with a wall thickness of 9-11mm. It is made of a pipe body and a joint by friction welding. The joints are divided into three types according to the thickening method: internal thickening, external thickening, and internal and external thickening. The thread buckle type is divided into four types: internal flat (IF), through-hole (FH), regular (REG), and digital (NC). According to the length and outer diameter, it can be divided into different specifications to adapt to various drilling conditions.
Choosing the right drill pipe will have more effects than you can imagine
Choosing the right drill pipe is of great significance to the efficient and safe development of drilling operations. From the perspective of operational efficiency, the appropriate drill pipe can work well with the drill bit and drilling rig, smoothly transmit power, ensure the stable and continuous drilling process, and significantly shorten the drilling cycle.
In terms of cost control, high-quality drill pipes with appropriate specifications are not only durable, which can reduce the frequency of replacement and lower material costs, but also reduce indirect costs such as labor and equipment rental due to efficient operations.
In terms of safety, drill pipes that meet standards and are of reliable quality are not prone to breakage or deformation when subjected to high pressure, high torque, and strong vibration. This greatly reduces the risk of underground accidents and ensures the safety of workers’ lives and the property of the company.
In addition, suitable drill pipes can reduce the extra loss of drilling rigs and other equipment, extend the overall service life of the equipment, reduce the cost of equipment maintenance and replacement, and lay a solid foundation for the long-term stable operation of the enterprise. It can be seen that choosing the right drill pipe model is a key link that cannot be ignored in drilling operations.
The following table shows you common drill pipe models and applicable scenarios:
Drill pipe model |
diameter(mm) |
Applicable geological conditions |
Recommended drilling rig types |
DZ40 - 42 |
42 |
Soft soil layer, ordinary soil layer |
Small rotary drilling rigs, some geological exploration drilling rigs |
DZ50 - 50 |
50 |
Various soil layers and soft rocks |
Medium-sized rotary drilling rigs, most anchor drilling rigs |
R780 - 60 |
60 |
Medium hard rock, hard rock |
Large rotary drilling rigs, mining drilling rigs |
R780 - 89 |
89 |
Hard rock, complex geology |
Large engineering drilling rigs, special geological exploration drilling rigs |
How to Choose the Right Model of Drill Pipes?
Choosing the right drill pipe model requires comprehensive consideration of many factors. The first is the purpose, which is determined by the actual situation such as drilling depth and geological conditions. For shallow hole operations or areas with simple geological conditions, smaller drill pipes can be selected; for deep well operations and complex geological structures, high-strength, large-sized drill pipes are required.
In terms of materials, drill pipes are made of various materials, including carbon steel, alloy steel, etc. Carbon steel has high strength, weak corrosion resistance, and low price; alloy steel has excellent strength and corrosion resistance, but the cost is higher. It should be determined based on actual needs and budget.
The manufacturing process has a profound impact on the quality and performance of drill pipe. High-quality processes can enhance the strength and corrosion resistance of drill pipe and extend its service life. For example, friction welding can make the drill pipe have high bending strength and strong welding.
In addition, the length and diameter should be selected based on the drilling depth, operating environment and drilling rig specifications. Large diameter drill pipes have high rigidity, but are heavy and inconvenient to transport and operate; long drill pipes can drill deep holes, but are troublesome to splice and disassemble. In short, the above factors should be fully considered when selecting drill pipes, and if necessary, consult professionals to ensure that the selected drill pipes meet the needs of the operation.