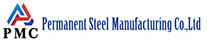
316 stainless steel pipe is a nickel-molybdenum alloy stainless steel pipe with excellent corrosion resistance and high temperature resistance. It is widely used in chemical, petroleum, medicine, food and other fields. Its chemical composition includes elements such as nickel, molybdenum, and chromium, which can resist corrosion from corrosive media such as acids and alkalis, so it is called "acid-resistant stainless steel pipe."
316 stainless steel pipes are usually divided into two types: welded pipes and seamless pipes. Different types of pipes have different outer diameters, wall thicknesses, lengths and other dimensions. For example, the outer diameter of 316 stainless steel welded pipes ranges from 6mm-530mm, and the wall thickness ranges from 0.5mm-45mm.
316 stainless steel pipes production steps
1. Material selection
Cold rolled stainless steel strip is used as raw material, and the surface condition is BA grade. Before the steel belt is put into use, it must be inspected in detail. Inspection items include: thickness, width, edge quality, appearance and physical properties. If necessary, the grain size of the raw material should be checked and it can be used for production only after passing the inspection.
2. Steel strip unwinding
Before the steel strip enters the welding pipe unit, it is necessary to use a steel strip unwinder to unwind the steel strip. A leveling mechanism is added to level the steel strip to ensure that the steel strip enters the forming part of the welding pipe unit in a straight state and the bending forming of the steel strip is completed smoothly.
3. Tube forming
The continuous roll bending equipment is used to continuously roll-bend the steel strip to form an open tube blank. The steel strip needs to pass through the joint action of the inlet module, rough rolling module and closing module of the welded pipe unit.Each module uses different types of rollers to bend different parts of the steel strip, and finally gradually bends the steel strip from a flat surface to form an open tube billet, ready for welding into 304 stainless steel tubes.
4. Continuous welding
The steel strip is made into an open tube blank after passing through a continuous roll bending forming unit. Use TIG welding equipment to perform continuous welding to make round pipes. Argon is used as a protective gas during welding to prevent the weld from coming into contact with oxygen and oxidizing before solidification and cooling.The argon gas is introduced into the tube to protect the internal weld, and the argon gas introduced into the welding gun is used to protect the tungsten electrode. An argon protective layer is formed around the molten pool to protect the molten pool and weld from oxidation.
5. Weld leveling
Due to the impact of welding current and the influence of gravity, the internal weld of stainless steel pipes will bulge and the external weld will be concave. These problems will not have any impact if used in ordinary low-pressure fluid environments. If used in high temperature, high pressure, high speed fluid environment, it will cause usage problems. Special weld leveling equipment must be used to eliminate this defect.
6. Online heat treatment
During the roll-bending process of the steel strip, work hardening will occur, which is not conducive to the subsequent processing of the pipe, especially the bending process. During the welding process, there will be welding stress at the weld, which will cause cracking hazards during later use, which requires heat treatment.
At present, the commonly used heat treatment process is bright solution treatment under hydrogen protective atmosphere. The 304 stainless steel pipe is heated to above 1050°. After a period of insulation, the internal organizational morphology changes to form a uniform austenite structure. Under the protection of hydrogen atmosphere, oxidation does not occur.
7. Sizing and finishing
The outer diameter of the welded pipe will deform during the welding and heat treatment process, causing the outer diameter to fail to meet the use requirements and requiring sizing and finishing. The commonly used sizing and finishing unit consists of 4 sets of flat rollers and 4 sets of side rollers. The flat rollers are designed to be flat ovals (or circles), and the side rollers are designed to be upright ovals (or circles). The sizing amount depends on the outer diameter and wall thickness of the pipe, and is generally within the range of 0.20 to 0.50 mm. After sizing and finishing, the outer diameter tolerance of the tube can be controlled within ±0.05mm, which can fully meet the accuracy requirements of use.
8. Online flaw detection
Since welds are subjected to a certain pressure and require a certain degree of reliability, it is difficult to detect internal defects of welds by relying solely on pressure testing. Online eddy current testing or ultrasonic testing can be used to perform 100% detection in real time online. The welding status can be corrected at any time according to the alarm information to reduce the production of defective products.
9. Cut to size
Use online cut-to-length equipment to cut to length according to the length required by the customer. Peel cutting (chip-free) technology can be used. Compared with chip cutting, chip-free cutting has the characteristic of no cutting burrs, and deburring of the port is not required in the later stage.
10 Straightening
The straightness of the welded pipe produced by the roll forming unit cannot meet the use requirements. Generally, the straightness of such welded pipes needs to be controlled at 0.10/100mm. A straightening machine is needed to straighten the welded pipe to meet the required product requirements.
11. Pressure test
Use an automatic static water pressure tester to perform a pressure test on 316 stainless steel pipes. Loading, flushing, pressure testing, and unloading are all completed automatically. After maintaining pressure for a certain period of time, unqualified welded pipes are sorted out using the pressure difference method.
12. Clean and dry
After the welded pipe is machined, it needs to be cleaned and dried to remove the coolant, oil and other pollutants remaining on the inner or outer wall of the pipe, and then dried with hot air to prevent rust during transportation and storage. Finally, the stainless steel pipes are inspected and packaged before they can be shipped out.
The above is the production process of 316 stainless steel pipe. The production process includes a series of processes such as material selection, uncoiling, tube blank forming, continuous welding, and weld leveling.