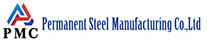
1. Seamless steel pipe-folding
It is a linear or spiral, continuous or discontinuous state that exists on the outer or inner surface of seamless steel pipe. The main reason for the folding is poor quality of the pipe material, folding itself, or inclusions, serious scratches and cracks on the surface, edges and corners in the grinding place, and folding after drawing. In order to avoid folding, the quality of the pipe material should be improved and attention should be paid to inspection and grinding.
2. Seamless steel pipe-crack
3. Seamless steel pipe-scratches
The inner and outer surfaces of the steel pipe were not removed in time due to defects such as folding and warping. In the subsequent processing, thin slices that could not be separated from the metal substrate were formed. Some of them were lumpy, discontinuous, and rooted or not rooted on the pipe wall, but they could not peel off naturally. , Called scarring. Surface defects must be checked and removed in time to eliminate scars.
Other supplementary information:
9. Inclusions
It is manifested as non-metallic inclusions embedded in the surface or surface cracks of the steel pipe. The inclusions are generally brought by the smelting, casting, hot working or heat treatment process, and are pressed into the surface when the tube blank is heated or the steel tube is annealed. The inspection should be strengthened in the relevant process and dealt with in a timely manner.
10. Diameter out of tolerance
The main reasons for the out-of-tolerance diameter are improper mold matching during cold working, insufficient mold hardness, or ignoring the change in the size of the extubation mold due to wear. Excessive reduction of the straightening roller during the straightening process will also cause the diameter of the steel pipe to become smaller.
11. Wall thickness out of tolerance
The main reasons for the excessive wall thickness are improper cold working mold matching, insufficient mold hardness, insufficient wear resistance, or ignoring the change in mold size due to wear and tear. Incorrect, the position of the mandrel is not adjusted properly when the short mandrel is drawn using the curved outer die and the tapered mandrel—before or after. In order to prevent the wall thickness from being out of tolerance, the mold should be correctly matched and the position of the mandrel should be adjusted correctly. The wall thickness change of the steel pipe in the emptying pass should be estimated accurately.
12. Uneven wall thickness
The main reasons for the uneven wall thickness of the steel pipe are: the uneven wall thickness of the tube blank is too large, the drawing line and the axis of the steel pipe are inconsistent during drawing, and the die holes of the mandrel and the drawing die are elliptical. In order to reduce the uneven wall thickness of the steel pipe, the uneven wall thickness of the pipe material should be as small as possible, and at the same time, the mold should be carefully checked and the pipe pulling machine should be adjusted.
13. Ellipse
That is to say, the die section of the steel pipe is oval, and the diameters on the same section are different. The difference between the maximum outer diameter and the minimum outer diameter is called ellipticity. During the drawing process, a drawing die with an oval die hole is used, or the two ends of the steel pipe are bent too much when straightening, and the steel pipe moves up and down during the straightening process, the steel pipe is stuck when the outer diameter is too large, and the steel pipe is stuck when pushed in. Excessive tail swing and uneven distribution of reduction between pairs of straightening rolls can cause this defect. If the defect occurs due to the ellipse of the die hole, the tube film should be replaced; if it is formed during the straightening process, the cause should be found and eliminated in time.
14. Bend
When the steel pipe rolls on the plane or is close to the ruler, there is a gap, which is called bending. The thinner the steel pipe, or the lower the strength, the easier it is to bend under the action of external force. In the process of processing, due to improper hoisting or improper stacking, the positive electrode is prone to bending, and in severe cases, the steel pipe may be deformed, resulting in exceptional ovality.
15. Bevel cut
When the end of the steel pipe is processed, the processing surface is not perpendicular to the axis of the steel pipe. It may be caused by the improper installation of the tool, or the skewness of the steel pipe when it enters the processing area.
16. Welding flash
There are irregular, roughly smooth surface protrusions on the surface of the steel pipe near the weld zone, called weld flashes. Mainly due to improper protection of the welding area, the electric spark is shot to the surface of the steel pipe.
17. Glitch
After the end of the steel pipe is processed, there will be a whole circle or part of the residual jagged flakes in the circumferential direction, and this defect is called burr. Mainly due to insufficient machining tool accuracy or improper tool installation.
Tips: ERW welded pipe is formed by rolling strip and welding the seam, with tighter dimensional tolerances and less weight. The weld seam is heat treated after welding that no untempered martensite remains, and the weld flash can be removed from both inner and outer surfaces.
ASTM A53 GR.B ERW steel pipe is a typical carbon steel pipe. It is largely used to convey fluids at low / medium pressures such as oil, gas, steam, water, air and also for mechanical applications.