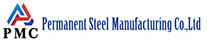
Es una especie de línea recta o espiral, estado continuo o discontinuo que existe en la superficie exterior o interior de la tubería de acero sin costura. El motivo principal del plegado es la mala calidad del material de la tubería, el plegado o las inclusiones, los rasguños y grietas graves en la superficie y los bordes y esquinas en el lugar de esmerilado, que se doblarán después de ser estirados. Para evitar el plegado, se debe mejorar la calidad del material de la tubería y se debe prestar atención a la inspección y el esmerilado.
Se refiere a las pequeñas fisuras en las superficies internas y externas de los tubos de acero sin costura que se distribuyen en líneas rectas o espirales, con una profundidad de 1 mm o más, y son continuas y discontinuas. Según el análisis de Permanent Steel Manufacturing Co., Ltd, la causa es: la pieza en bruto del tubo laminado en caliente tiene burbujas subcutáneas e inclusiones subcutáneas, y hay grietas o picaduras profundas en la tubería de acero antes del estirado. Durante los procesos de laminado en caliente o estirado en frío Ocurrieron rayones o rayones longitudinales durante la operación. La prevención de la formación de grietas también radica en mejorar la calidad del tubo en bruto y fortalecer la inspección y rectificado del material del tubo. Al mismo tiempo, se deben evitar picaduras, rayones y rayones durante el proceso de producción de estirado en frío.
Las superficies internas y externas de la tubería de acero no fueron removidas a tiempo debido a defectos como el plegado y deformación. En el procesamiento posterior se formaron láminas delgadas que no pudieron separarse del sustrato metálico. Algunas de ellas eran grumosas, discontinuas y enraizadas o no enraizadas en la pared de la tubería, pero no podían desprenderse naturalmente , Llamado cicatrices. Los defectos de la superficie deben revisarse y eliminarse a tiempo para eliminar las cicatrices.
Otra información complementaria:
9. Inclusiones
Se manifiesta como inclusiones no metálicas incrustadas en la superficie o en las grietas de la superficie de la tubería de acero. Las inclusiones generalmente provienen del proceso de fundición, vaciado, trabajo en caliente o tratamiento térmico, y se presionan en la superficie cuando se calienta la pieza en bruto del tubo. o el tubo de acero está recocido. La fiscalización debe ser fortalecida en el proceso correspondiente y tratada en tiempo y forma.
10. Diámetro fuera de tolerancia
Las razones principales por las que el diámetro está fuera de tolerancia son la adaptación inadecuada del molde durante el trabajo en frío, la dureza insuficiente del molde o la ignorancia del cambio en el tamaño del molde de extubación debido al desgaste. La reducción excesiva del rodillo enderezador durante el proceso de enderezamiento también hará que el diámetro de la tubería de acero se reduzca.
11. Espesor de pared fuera de tolerancia
Las razones principales del espesor de pared excesivo son la adaptación incorrecta del molde de trabajo en frío, la dureza del molde insuficiente, la resistencia al desgaste insuficiente o ignorar el cambio en el tamaño del molde debido al desgaste.Incorrecto, la posición del mandril no se ajusta correctamente cuando el corto el mandril se dibuja utilizando el troquel exterior curvo y el mandril cónico, antes o después. Para evitar que el grosor de la pared esté fuera de tolerancia, el molde debe coincidir correctamente y la posición del mandril debe ajustarse correctamente. El cambio de espesor de pared de la tubería de acero en el paso de vaciado debe estimarse con precisión.
12. Espesor de pared desigual
Las razones principales del grosor desigual de la pared de la tubería de acero son: el grosor desigual de la pared del tubo en blanco es demasiado grande, la línea de dibujo y el eje de la tubería de acero son inconsistentes durante el dibujo, y los orificios de troquel del mandril y el los troqueles de dibujo son elípticos. Para reducir el grosor desigual de la pared de la tubería de acero, el grosor desigual de la pared del material de la tubería debe ser lo más pequeño posible y, al mismo tiempo, el molde debe revisarse cuidadosamente y la máquina extractora de tubería debe ajustarse.
13. Elipse
Es decir, la sección de la matriz de la tubería de acero es ovalada y los diámetros en la misma sección son diferentes.La diferencia entre el diámetro exterior máximo y el diámetro exterior mínimo se denomina elipticidad. Durante el proceso de trefilado, se usa un troquel de trefilado con un orificio de troquel ovalado, o los dos extremos de la tubería de acero se doblan demasiado cuando se endereza, y la tubería de acero se mueve hacia arriba y hacia abajo durante el proceso de enderezamiento, la tubería de acero se atasca cuando el diámetro exterior es demasiado grande y la tubería de acero se atasca cuando se empuja hacia adentro. El giro excesivo de la cola y la distribución desigual de la reducción entre los pares de rodillos enderezadores pueden causar este defecto. Si el defecto se produce debido a la elipse del orificio de la matriz, se debe reemplazar la película del tubo; si se forma durante el proceso de enderezamiento, se debe encontrar la causa y eliminarla a tiempo.
14. Doblar
Cuando la tubería de acero rueda en el plano o está cerca de la regla, hay un espacio, que se llama flexión. Cuanto más delgada sea la tubería de acero, o menor sea la resistencia, más fácil será doblarla bajo la acción de una fuerza externa. En el proceso de procesamiento, debido a una elevación o apilamiento incorrectos, el electrodo positivo tiende a doblarse y, en casos severos, la tubería de acero puede deformarse, lo que resulta en una ovalidad excepcional.
15. Corte biselado
Cuando se procesa el extremo de la tubería de acero, la superficie de procesamiento no es perpendicular al eje de la tubería de acero. Puede deberse a la instalación incorrecta de la herramienta o al sesgo de la tubería de acero cuando ingresa al área de procesamiento.
16. Flash de soldadura
Hay protuberancias superficiales irregulares y aproximadamente lisas en la superficie de la tubería de acero cerca de la zona de soldadura, llamadas rebabas de soldadura. Principalmente debido a la protección inadecuada del área de soldadura, la chispa eléctrica se dispara a la superficie de la tubería de acero.
17. Fallo
Después de procesar el extremo de la tubería de acero, habrá un círculo completo o parte de las escamas irregulares residuales en la dirección circunferencial, y este defecto se denomina rebaba. Principalmente debido a una precisión insuficiente de la herramienta de mecanizado o a una instalación incorrecta de la herramienta.
Consejos: la tubería soldada ERW se forma enrollando una tira y soldando la costura, con tolerancias dimensionales más estrictas y menos peso. La costura de soldadura se trata térmicamente después de la soldadura para que no quede martensita sin templar, y el rebaba de soldadura se puede quitar tanto de las superficies internas como externas.
La tubería de acero ASTM A53 GR.B ERW es una tubería típica de acero al carbono. Se utiliza principalmente para transportar fluidos a presiones bajas/medias como petróleo, gas, vapor, agua, aire y también para aplicaciones mecánicas.