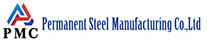
In the petroleum industry, seamless pipes can be called "behind-the-scenes heroes", silently playing an irreplaceable and key role. In the petroleum industry, seamless steel pipes are often used in high pressure, high temperature and corrosive environments. Therefore, their quality is directly related to the safety and stability of key links such as oil extraction, transportation, storage and refining. However, due to various factors, seamless steel pipes may have some quality problems in actual applications, affecting their performance and service life. The following summarizes the common quality problems and causes of seamless steel pipes in the petroleum industry.
1. Mechanical properties are unqualified
Seamless pipes in the petroleum industry often need to withstand high pressure, strong torque and high temperature. If the mechanical properties of the steel pipes are not up to standard, it may cause the pipelines to rupture or deform, thus affecting the normal operation of the equipment.
Common problems
Insufficient strength: The tensile strength, yield strength or hardness of the steel pipe does not meet the requirements and cannot withstand the design pressure.
Poor ductility: The pipe has poor ductility and is prone to cracks during operation.
Poor fatigue resistance: When subjected to pressure for a long time or repeated loading, the pipe may suffer fatigue cracks or rupture.
Main reasons
Uneven alloy composition or improper smelting during the production process results in the strength and toughness of the steel pipe failing to meet standard requirements. Improper heat treatment process, such as inaccurate heat treatment temperature control, may cause the hardness of the steel pipe to be too high or too low, thus affecting its strength and durability.
2. Internal and external surface defects
The surface quality of seamless pipes directly affects their performance, especially in the petroleum industry, where surface defects may cause serious accidents such as pipeline bursts and leaks under high pressure and temperature.
Common problems
Cracks, scratches, pits: The surface of seamless pipes may have cracks, scratches or pits, especially in high temperature environments. These surface defects may cause local stress concentration, thereby inducing cracks or ruptures.
Oxide scale and rust: During the manufacturing and storage process, oxide scale or rust may form on the surface of the steel pipe, affecting the corrosion resistance of the pipeline.
Too high surface roughness: If the surface roughness of the seamless steel pipe is too high, it will affect its friction coefficient during use, thereby increasing the wear of the pipe during use and reducing its service life.
Main reasons
Improper operation during processing: Improper processes such as cold drawing, pickling, and hot rolling may lead to surface defects.
Improper storage: There are no moisture-proof and corrosion-proof measures when storing seamless steel pipes, causing surface corrosion or oxidation.
3. Welding joint problems
Although seamless steel pipes themselves have no welds, in the petroleum industry, pipelines often need to be welded and connected. If the welding quality is unqualified, it will directly affect the safety of the entire pipeline system.
Common problems
Weld cracking: Cracks may occur during the welding process, especially under high temperature and high pressure working conditions, and the welded joints are susceptible to stretching and corrosion.
Welding pores and slag inclusions: During welding, pores or slag inclusions may cause the strength of the weld to decrease, affecting the pressure-bearing capacity and sealing performance of the pipeline.
Main reasons
Improper welding process: welding operation is not standardized, welding materials, temperature control or welding speed do not meet the standards, resulting in welding defects.
Unqualified welding materials: The quality of the welding materials used is poor, or the shielding gas during welding is insufficient, which can easily lead to defects in the weld.
4. Size is not up to standard
The dimensional accuracy of seamless steel pipes is crucial for pipeline installation in the petroleum industry. If the outer diameter, wall thickness or length of the pipe does not meet the standards, it may lead to installation difficulties, loose joints, and even affect the safety of the entire pipeline system.
Common problems
Outer diameter is unqualified: The outer diameter of the pipe has a large deviation, which affects the connection and installation.
Uneven wall thickness: Uneven wall thickness may reduce the pressure-bearing capacity of the pipe under high-pressure environment, and some parts are prone to breakage or bursting.
Inconsistent length: If the length of the pipe is unqualified, too many joints may be generated during on-site installation, increasing the risk of leakage.
Main reasons
Unstable production process: Imprecise temperature control during hot rolling and cold drawing, or uneven speed during stretching, will lead to dimensional deviation.
Uneven cooling: Uneven temperature during the cooling process of the steel pipe will also affect the dimensional accuracy of the steel pipe.
5. Corrosion resistance does not meet the standard
Seamless steel pipes in the petroleum industry often need to withstand corrosive media such as strong acids, brine, chlorides, etc., so their corrosion resistance is crucial. If the corrosion resistance of the steel pipe is unqualified, it is easy to cause pipeline corrosion, leakage and pipe burst.
Common problems
Intergranular corrosion: Steel pipes are prone to intergranular corrosion in environments with high temperatures and corrosive media such as chlorides, resulting in reduced strength and toughness of the pipes.
Local corrosion: such as pitting corrosion and crevice corrosion, which are prone to form cracks on the surface of steel pipes, affecting the long-term safety of the pipeline.
Main reasons
Improper alloy element ratio: Insufficient content of elements such as nickel, chromium, and molybdenum in the alloy composition leads to poor corrosion resistance.
Unqualified heat treatment: Improper heat treatment process fails to effectively improve the intergranular corrosion and corrosion resistance of the steel pipe.
Improper storage: If effective anti-corrosion measures are not taken during the storage of seamless steel pipes, especially in humid and corrosive environments, corrosion is prone to occur.
Read more: How to Distinguish the Materials of Seamless Pipes and Galvanized Steel Pipes?