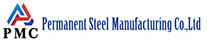
The drill pipe is a steel pipe with a threaded tail, which is used to connect the surface equipment of the drilling rig and the drilling and grinding equipment or bottom hole device at the bottom of the well. Drill pipes are made of both seamless tubes and welded pipes. The purpose of the drill pipe is to carry drilling mud to the drill bit and to raise, lower or rotate the bottom hole device together with the drill bit.
Specifications and dimensions
1. Outer diameter: The outer diameter of the drill pipe varies, and the common ones are 60mm, 73mm, 89mm, 114mm, 127mm, 140mm, 168mm, 219mm, etc. Drill pipes with different outer diameters are suitable for different drilling projects and formation conditions. Generally speaking, deep well drilling may use drill pipes with larger outer diameters to withstand greater pressure and torque.
2. Wall thickness: Wall thickness is also an important factor affecting drill pipes performance. Common wall thickness specifications include 6mm, 7mm, 8mm, 9mm, 10mm, 12mm, 13mm, 14mm, 15mm, 16mm, 17mm, 18mm, 19mm, 20mm, etc. The choice of wall thickness should be determined according to factors such as drilling depth and formation pressure. The deeper the drilling depth and the greater the formation pressure, the thicker the wall thickness of the drill pipe is.
3. Length: The length of a single drill pipe is generally around 9-12 meters. In actual drilling operations, multiple drill pipes will be connected through joints to form a drill string as needed to achieve the required drilling depth.
What are the common problems and solutions for drill pipes inspection?
Drill pipes inspection is an important part of oilfield drilling operations, and its quality is directly related to drilling safety and efficiency. Some common problems may occur during the drill pipe inspection process. Here we introduce some common problems and their solutions.
1. There are cracks on the drill pipe surface: Cracks on the drill pipe surface may be caused by excessive use or improper operation. The solution is to repair the cracked part or replace the drill pipe with a new one.
2. Drill pipes bending: Drill pipes bending will affect the progress and quality of drilling. The solution is to adjust the drilling parameters in time to prevent the drill pipe from bending too much and causing more problems.
3. Drill pipes breakage: Drill pipes breakage is a more serious problem that will bring safety hazards and production losses. The solution is to improve the technical level of operators and do a good job of maintenance of drill pipes to avoid breakage.
4. Drill bit sticking: Drill bit sticking can lead to increased drilling time and costs. The solution is to clean and maintain the drill in time to keep it unobstructed and avoid jamming.
5. Drilling losses: Drilling losses refer to the loss of oil, gas or mud from the wellbore during the drilling process. The solution is to adjust the drilling parameters in time to reduce the possibility of loss and ensure the smooth progress of drilling.
6. Drill pipes section failure: Drill pipes section failure can result in insufficient well depth and reduced drilling quality. The solution is to replace the failed drill pipes section in time to ensure the integrity of the entire drill pipes.
7. Drill pipes surface corrosion: Rust and pitting appear on the surface of the drill pipes. Corrosion can cause the pipe wall to become thinner and weaken the strength of the drill pipe. In severe cases, it may cause perforation of the drill pipe, affecting its sealing and bearing capacity, and thus causing drilling accidents.
The solution: For minor surface corrosion (such as the pit depth does not exceed 10% of the drill pipe wall thickness), the corroded parts can be first derusted with a rust remover, and then protective materials such as anti-corrosion paint can be applied to delay further development of corrosion.
If the corrosion is severe (the depth of the corrosion pit exceeds 10% of the drill pipe wall thickness), the drill pipe should be replaced, because the severely corroded drill pipe can no longer guarantee the safety of drilling operations.
Read more: Common Drill Pipe Connection