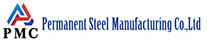
The production process of thick-walled seamless steel pipes can be divided into four basic methods: cold drawing, cold rolling, hot rolling and hot expansion. According to the purpose, it is divided into seamless steel pipes for structures; seamless steel pipes for transportation; seamless steel pipes for boilers; seamless steel pipes for boilers with high pressure; seamless steel pipes for fertilizer equipment with high pressure; seamless steel pipes for geological drilling; seamless steel pipes for oil drilling; seamless steel pipes for oil cracking; seamless steel pipes for ships; cold-drawn and cold-rolled precision seamless steel pipes; various alloy pipes.
Seamless steel pipes are indicated by outer diameter and wall thickness. Thick-walled seamless steel pipes are mainly used for mechanical processing, coal mines, hydraulic steel, and many other purposes.Thick-walled seamless steel pipes are mostly used in coal mining, mechanical processing, petroleum, light industry, etc.
So what are the characteristics of cast thick-walled seamless steel pipes?
1. The key considerations during the production process are its process structure and performance. On the one hand, we need to improve productivity, on the other hand, we need to ensure quality. During production, the integrity of the sample must be checked to ensure that it is used without defects. If there are defects, they must be repaired before they can be used. Pay attention to the knocking force when removing the mold. The aluminum mold should be knocked with a wooden block to reduce the damage to the aluminum mold.
2. When producing thick-walled seamless steel pipe fittings, the quality of the furnace and packaged materials needs to be strictly controlled, and their composition, block size and physical and chemical properties need to be inspected and accepted as required.
3. Through inspection, find the defects of thick-walled seamless steel pipes, find and analyze the causes, and take timely measures to reduce the occurrence of defects.
4. Before pouring, the casting water should be inoculated and slag removed. The process should be continuous and stable to avoid sand holes caused by sand washing. When there is a fire, the leaking casting water should be blocked in time and the casting water should be replenished to reduce defects such as cold shut and insufficient pouring.
5. The performance of molding sand will directly affect the quality of thick-walled seamless steel pipes, so it should have good air permeability, wet strength, fluidity, plasticity and yieldability.
6. When the clay content is the same, bentonite has higher hot wet tensile strength than ordinary clay. Adding an appropriate amount of coal powder, sawdust, etc. to wet clay sand can improve the ability to resist sand inclusion, prevent sand inclusion and sticking, and obtain pipe fittings with smooth surface. The moisture content of the molding sand is set at about 6% to give it better comprehensive performance.
7. To obtain thick-walled seamless steel pipes with good surface finish, the sand on the surface can be removed by cleaning the drum and shot blasting can also be performed. The sticky sand on the non-processed surface needs to be cleaned to prevent affecting the use of the pipe fittings.
8. For the dry mold drying process, the operation procedures must be followed and the drying time should be more than 8 hours to prevent defects such as sand and pores caused by incomplete drying.
9. The pipe fittings need to be fully cooled before they can be removed from the mold, which is generally required to be no less than 3 hours. If the time is too short, the surface will be chilled, making the hardness higher and making it difficult to cut. When thick-walled seamless steel pipe fittings are large, thermal cracks may occur and internal stress may be greater, which may easily cause deformation and affect the external dimensions.
Read more: Cutting Methods of Thick-walled Seamless Steel Pipes