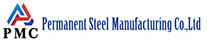
Oil casing pipe is a steel pipe used to support the wall of oil and gas wells to ensure the normal operation of the entire oil well during the drilling process and after completion. Each well uses several layers of casing according to different drilling depths and geological conditions. After the casing is lowered into the well, cement is used for cementing. Unlike oil pipes and drill pipes, it cannot be reused and is a one-time consumable material. Therefore, the consumption of casing accounts for more than 70% of all oil well pipes.
Anticorrosion Countermeasures for Oil Casing Pipes
1. First of all, do a good job of meeting water quality standards, and strictly monitor and manage water quality. Carry out decontamination and injection, strengthen the cleaning of main water pipelines, achieve water quality standards in stations and bottoms, and reduce the introduction of corrosion sources into the annular space;
2. For water injection wells that have been newly put into production, adopt annulus protection fluid mainly based on dosing and sterilization, and form a system to do so on a regular basis;5. It is not recommended to use cathodic protection and coated casing until the corrosion in the casing pipe of the injection well is not effectively controlled.
Anti-corrosion Technology of Oil Casing Pipes
1. Cement sealing anti-corrosion techniques
In the earliest period, it was analyzed that the key to the casing damage was that the cement could not be restored and the water layer outside the formation was not completely sealed, forming corrosive gases. Water layer corrodes the casing surface to form corrosion. After adopting this technology, the degree of casing corrosion has been reduced, but it has not been completely prevented, so the anti-corrosion function of the casing pipe has not been improved from the spring.
2. Use corrosion-resistant alloy pipe
Since 2000, the anti-corrosion solution for offshore oil casing has begun to seek treatment solutions from the material to improve the anti-corrosion function of oil casing pipes and completely solve the corrosion problem of oil casing. Over the years, through laboratory tests, under certain temperature, pressure and corrosive gas conditions, 1Cr, 3Cr, 9Cr, 13Cr and other chromium-containing pipes have been evaluated, and a set of corrosion-resistant sheet shells suitable for offshore oil and gas fields has been developed.
3. Injection of corrosion inhibitor
From the completion process, if the formation contains oily corrosive gases, chemical preservatives are added to the well fluid to prevent scaling, wax and corrosion. Therefore, it is also a common practice to use chemical methods to protect oil casing pipes abroad. Depending on the oil and gas field itself, intermittent or continuous injection of corrosion inhibitors can be used for corrosion prevention. The injection amount also varies according to the corrosive environment of the oil and gas field. Due to the increasing demand for adding corrosion inhibitors, on the one hand, the cost is high, but it will also have a positive impact on on-site production.
4. Use anti-corrosion coated pipes
For oil casing pipes, anti-corrosion coating to prevent corrosion from corrosive gases is also a useful anti-corrosion method. Some oil fields use nitriding technology to prevent corrosion inside and outside the oil pipe, which has good wear resistance. However, this method of internal and external wall corrosion protection will accelerate the corrosion of the inner wall of the casing to a certain extent. Some oil and gas fields use epoxy powder coatings, titanium nano coatings, epoxy ester phenolic coatings and other methods for corrosion protection.