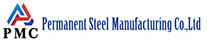
The well casing pipe is a tubular metal product used in various wellbores such as oil wells, gas wells, and water wells. It is installed along the wellbore wall and plays an important role in supporting the well wall, isolating different strata, protecting equipment in the well, and preventing well wall collapse. Well casing pipes face the threat of many corrosion factors in the complex underground environment, such as formation water, hydrogen sulfide, carbon dioxide, etc. It is very important to take effective anti-corrosion measures. The following are some common anti-corrosion measures for well casing pipes:
Selection of corrosion-resistant materials
1. Alloy steel material: Alloy steel containing alloy elements such as chromium (Cr), nickel (Ni), and molybdenum (Mo) is selected as the well casing material. Alloy steels such as 316 stainless steel (containing about 16% - 18% chromium, 10% - 14% nickel, and 2% - 3% molybdenum) have better corrosion resistance than ordinary carbon steel and are suitable for oil wells, gas wells, etc. with severe corrosive environments.
For high-sulfur oil and gas wells, sulfur-resistant alloy steel can be selected. Through special alloy ratio design, it can effectively resist the corrosion of hydrogen sulfide gas on the casing pipe and prevent sulfide stress corrosion cracking and other problems.
2. Coating Material:
It is also a common method to apply anti-corrosion coating on the surface of well casing pipes. Common coatings include epoxy coating, polyurethane coating, etc.
The thickness of the coating is generally determined according to the specific corrosion environment and usage requirements, usually between tens of microns and hundreds of microns.
Use of corrosion inhibitors
The corrosion inhibitor is injected into the wellbore through the wellhead to form a protective film on the surface of the well casing pipes, thereby slowing down the corrosion rate. There are many types of corrosion inhibitors, which can be divided into anodic corrosion inhibitors, cathodic corrosion inhibitors and mixed corrosion inhibitors according to their mechanism of action.
Cathodic protection
1. Sacrificial anode protection: Sacrificial anode materials such as magnesium alloy, aluminum alloy, etc. are installed around the well casing pipe. These sacrificial anode materials are more active than the metal material of the well casing pipe. In the downhole environment, they will preferentially lose electrons and undergo oxidation reactions, thereby protecting the well casing pipe as a cathode.
2. Impressed Current Cathodic Protection:
An impressed current cathodic protection system is installed near the well casing pipe, including auxiliary anodes, DC power supplies and other equipment. This method can flexibly adjust the size of the protection current according to actual needs, and is suitable for oil wells with complex corrosion environments and high requirements for protection effects.
However, the design, installation and maintenance of the impressed current cathodic protection system are relatively complex and require professional personnel to operate. In addition, the size of the protection current and the corrosion state of the casing pipe must be monitored regularly to ensure the normal operation of the system.
Improve the wellbore environment
1. Control water quality:
In oil wells developed by water injection, the quality of the injected water is strictly controlled. Through filtration, deoxygenation, sterilization and other treatment measures, the content of suspended matter, dissolved oxygen, bacteria and other substances that may corrode the casing pipe in the injected water is reduced.
2. Reduce hydrogen sulfide and carbon dioxide levels:
For oil and gas wells containing hydrogen sulfide and carbon dioxide, some measures can be taken to reduce the content of these two gases in the wellbore. For example, the gas in the produced liquid can be separated as much as possible through gas-liquid separation equipment to reduce the contact between hydrogen sulfide and carbon dioxide and the casing pipe; or chemical absorption method can be used to absorb hydrogen sulfide and carbon dioxide with specific chemical reagents to reduce their concentration.
Regular inspection and maintenance
1. Corrosion detection: A variety of detection methods are used to regularly detect the corrosion of well casing pipes. Common detection methods include ultrasonic detection, magnetic particle detection, and radiographic detection. Based on the test results, the corrosion degree of the casing is evaluated to determine whether further anti-corrosion measures or maintenance, replacement, etc. are required.
2. Maintenance measures:
When slight corrosion is detected in the casing pipe , some targeted maintenance measures can be taken. For example, for surface corrosion, it can be repaired by rust removal, painting, etc.; for areas with severe local corrosion, repair welding and other methods can be used for treatment, but after repair welding, it is necessary to conduct another inspection to ensure the welding quality and corrosion resistance of the casing.
Regularly inspect and maintain the well casing pipe, establish a complete maintenance file, and record the situation of each inspection and maintenance, so as to timely grasp the corrosion dynamics of the casing pipe and provide a reference for subsequent anti-corrosion and maintenance work.
Read more: Advantages and Disadvantages of Well Casing Pipes