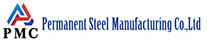
The introduction of well casing pipes
The well casing pipe is a tubular structure that is put into the well to support the well wall, protect the wellbore, isolate the formation, guide the fluid, etc. in oil and gas drilling projects and some groundwater well projects. It is usually made of steel and has different materials, specifications and connection methods to meet various well conditions and engineering requirements.
Well casing pipes have the following advantages:
1. Support the well wall: It can effectively prevent the well wall from collapsing, maintain the stability of the wellbore, ensure the safety of the drilling process and the normal production of oil wells, gas wells, etc. after completion. In areas with complex geological conditions, such as rock fracture zones and soft formations, the supporting role of the well casing pipe is particularly important to avoid drilling accidents and production interruptions caused by well wall instability.
2. Isolate strata: separate different strata to prevent fluids between layers from interfering with and flowing across each other. For example, in the oil layer casing pipe, the oil and gas layer can be isolated from other formations to ensure that the oil and gas can flow smoothly from the oil and gas layer to the ground, while preventing impurities such as formation water and rock particles from entering the oil and gas channel, thereby improving the production and quality of oil and gas.
3. Withstand pressure: It has high strength and pressure resistance, and can withstand the huge pressure from the formation and various external forces during the drilling process, such as drilling fluid pressure, rock pressure, etc. In high-pressure environments such as deep wells and ultra-deep wells, well casing pipes can ensure the integrity of the wellbore, prevent the casing pipe from being crushed or deformed, and ensure the smooth progress of oil and gas production.
4. Protect equipment: Protect underground drilling equipment, oil pipes, etc., reduce their direct contact and wear with the well wall rock, extend the service life of the equipment, and reduce maintenance costs during drilling and production.
5. Guiding fluid: providing channels for drilling fluid, cement slurry and other fluids to ensure their normal circulation and flow in the well. The circulation of drilling fluid helps to cool the drill bit, carry cuttings, etc., while the injection of cement slurry can achieve effective cementing between the casing pipe and the well wall, further enhancing the stability of the wellbore.
The disadvantages of well casing pipes mainly include the following points:
1. High cost: The production of well casing pipes requires the use of high-quality steel and other materials, and the manufacturing process is relatively complicated, resulting in relatively high costs. In addition, in some special environments, such as deep sea, high temperature and high pressure, higher performance casing materials are required, and the cost will increase further. For some small oil and gas fields or projects with limited economic conditions, the cost of well casing pipes may become one of the factors restricting its development.
2. Difficult installation: Installation of the well casing pipe requires professional equipment and technicians, and the operation process is relatively complicated. During the installation process, it is necessary to ensure that the casing pipe is tightly connected and well sealed, and at the same time ensure that parameters such as the verticality and concentricity of the casing pipe meet the requirements, otherwise it may affect the use effect and life of the casing pipe. In addition, in deep wells or under complex geological conditions, the difficulty of lowering the casing pipe will increase accordingly, and problems such as casing pipes jamming and casing pipes damage may occur.
3. Non-reusable: Generally speaking, the well casing pipe is a disposable consumable material and cannot be reused during the life cycle of a well. This means that a large amount of money needs to be invested in the purchase and installation of well casing pipes in the construction of each new well, increasing the overall cost of oil and gas development.
4. Susceptible to corrosion: In the harsh environment underground, the well casing pipe is easily corroded by various corrosive media, such as formation water, hydrogen sulfide, carbon dioxide, etc., which leads to thinning of the casing wall thickness, reduced strength, and even failure forms such as perforation and rupture, affecting the normal production of the well. In order to extend the service life of the casing pipe, corresponding anti-corrosion measures need to be taken, such as using corrosion-resistant materials, applying anti-corrosion coatings, implementing cathodic protection, etc., but these measures will also increase certain costs and workload.
Read more: Steel Well Casing Pipe Sizes