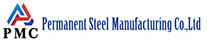
Stainless steel welded pipe, referred to as welded pipe, is a steel pipe made by welding steel or steel strip after being curled and formed by a unit and a die. The production process of welded steel pipe is simple, the production efficiency is high, the variety and specifications are many, and the equipment investment is small, but the general strength is lower than that of seamless tube.
In the process of processing and application of stainless steel welded pipes, welding spots are like a "cancer" that grows quietly and brings many adverse effects to the products. From the appearance, those dotted and dark welding spots greatly damage the originally smooth and bright surface of stainless steel. In a humid, acidic, alkali and other corrosive environments, stainless steel welded pipes with weld spots are like losing their protective armor and are easily corroded, thereby shortening their service life and even causing safety hazards.
Why do annoying weld spots appear?
1. Welding materials: poor quality welding wire, many impurities, or chemical composition does not match the parent material; the electrode is damp, and the water decomposes to cause metal oxidation.
2. Welding process: improper parameters such as welding current, voltage, speed, unstable arc, and more spatter; poor selection of welding methods, insufficient gas protection, and air intrusion.
3. Welding environment: air pollution, dust, oil, etc. adhere to the weld reaction; high environmental humidity, water decomposition produces hydrogen and oxygen, leading to pores and oxidation.
4. Parent material surface: impurities such as oil and rust on the surface, which are mixed into the weld when heated; untreated oxide film hinders metal fusion to form inclusions.
Take precautions to prevent welding spots from getting close to you
1. Weld spots are annoying, but there are ways to prevent them. First of all, we must ensure that the supply of protective gas is stable, the purity and flow of argon and helium should be accurately controlled, the gas supply device should be checked frequently, and the leakage or blockage should be prevented, and the welding area is always "guarded" by inert gas.
2. Adjustment of welding parameters is also critical. Reasonable matching of current, voltage, and welding speed, stable heat input, can prevent local overheating and reduce oxidation. Stainless steel welded pipes of different diameters and wall thicknesses have different adaptation parameters and need to be fine-tuned according to actual conditions.
3. Choosing the right welding material is the key. The composition of welding wire and welding rod should be in tune with the base material, with less impurities and ferrite, and element segregation is unlikely to occur, so there will naturally be fewer weld spots.
4. Cleaning before welding cannot be perfunctory. Oil, oxide scale, dust, etc. on the surface of stainless steel should be removed by chemical cleaning, mechanical grinding, etc. to prepare a "clean ground" for welding.
5. After welding, it is very important to control the cooling speed. Air cooling and water cooling can be used to help the weld pipe cool down quickly, shorten the contact time with oxygen, and make weld spots less likely to appear.
Weld spots have appeared, how to remove them quickly?
If weld spots have already appeared, don't panic, there are many tips to remove them.
Soak stainless steel weld spot cleaner for 5-20 minutes to quickly clean weld spots, oxide scale, etc. After washing, the surface is matte white.
Soak the washed steel in molten steel at room temperature for 10 - 30 minutes or even longer to remove the weld spots and complete the passivation at the same time, thus improving the corrosion resistance. It is suitable for workpieces with anti-corrosion requirements and convenient immersion. The surface is uniform silver-white after treatment. Apply the pickling passivation paste to the weld spot and let it stand for 5-20 minutes. It is the best choice for cleaning the surface of large stainless steel welded pipes, and then rinse with water.
The weld cleaning machine is also very powerful. It can handle large and small weld spots and pipes with different surfaces. After power is turned on, the ions in the electrolyte react chemically with the oxide skin to achieve cleaning and polishing in one step. Mechanical grinding is a traditional method. Grinding with grinding wheels or sandpaper can remove weld spots. Grinding wheels are suitable for large areas and rough processing, while sandpaper is used for fine areas. However, attention should be paid to the strength to prevent excessive wear.
Chemical pickling uses acidic solutions such as nitric acid and hydrofluoric acid to remove weld spots and contaminants. After pickling, it is necessary to thoroughly rinse and dry to prevent acid residue. Electrolytic polishing relies on electrochemical reactions. The welded pipe is immersed in an electrolyte and energized to dissolve oxides, making the surface smoother and more corrosion-resistant. These methods have their own advantages and disadvantages, and should be flexibly selected based on the actual welded pipe, production conditions, cost considerations, etc., to make the stainless steel welded pipe shiny again.
Read more: How to Deal with Accidental Cracking of Stainless Steel Welded pipes?