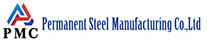
A fire tube boiler is a boiler whereby heated gasses flow from a flame through one or more tubes, flowing through a sealed water tube. The heat of the gasses is transmitted through thermal conduction through the tube walls, heating up the water and eventually producing steam. This boiler was used in the horizontal locomotive configuration on nearly all steam locomotives. This has a tubular container that holds the fire tubes and an extension to fit the one-end firebox. This firebox has an open foundation to have a wide area of the grate, stretching to create a rectangular or tapered structure outside the cylindrical container.
The only commodity used in boiler construction during most of the Victorian “era of steam” was the lowest quality wrought iron, with mounting by riveting. This iron was primarily sourced from specialist ironworks, such as those in the Celator Moor region (UK), known for the high nature of their rolled steel, which was ideal for use in essential applications such as increased-pressure boiler tubes. Technology innovation in the 20th century shifted towards steel usage of welded production, which is safer and more straightforward, which can be made quicker and with less labour. Wrought iron boiler tubes corrode even more gradually than their counterparts in conventional steel and are less prone to irregular pitting and stress corrosion. The longevity of older wrought-iron boiler tubes is far superior to that of welded steel boiler tubes.
Boiler tube material requirements:
The materials used for boiler tubes must be carefully selected to meet the following requirements:
(1) High temperature resistance and high strength
High-pressure boiler tubes are often exposed to high temperature and high pressure conditions during use. Under the action of high-temperature flue gas and water vapor, pipelines will oxidize and corrode. Steel pipes are required to have high lasting strength, high oxidation resistance, corrosion resistance and good structural stability. The working conditions of high-pressure boiler tubes are very harsh. They must work safely under high pressure, high temperature, and the erosion and corrosion of high-speed airflow, water flow, and gas for 10 to 20 years, or even longer.
(2)Thermal conductivity
Boiler tubes, especially high-pressure boiler tubes, are pipes used to transport high-temperature and high-pressure steam or hot water and play an important role. In the design and use of high-temperature boiler tubes, thermal conductivity is a very critical indicator.
Thermal conduction is the process by which heat is transferred from a high-temperature object to a low-temperature object. In high-temperature boiler tubes, heat conduction occurs mainly through conduction in the tube wall. The heat conduction characteristics of the pipe wall are related to the thermal conductivity of the material, wall thickness, pipe diameter and temperature gradient.
(3) Comply with standards: Materials must comply with safety and quality standards set by regulatory agencies such as ASTM, ASME or EN.
Common ASTM standards for boiler tubes include:ASTM A178 Boiler and superheater tubes for electric welding of carbon steel and carbon manganese steel boiler and superheater tubes. ASTM A178 is the same as ASME SA-178 and is a standard specification covering minimum wall thickness resistance welded pipe for boiler tubes, boiler flues, superheater flues, and minimum wall thickness made of carbon steel and carbon manganese steel.
ASTM A179 high-temperature boiler tube is a steel tube used in high-temperature environments with good pressure resistance and high-temperature strength. ASTM A179 high temperature boiler tube is a kind of seamless steel pipe, manufactured by heat treatment process, with the characteristics of high precision, high smoothness, high wear resistance and so on. This steel pipe is mainly used in high temperature and high pressure environments, such as boilers, heat exchangers, petroleum cracking units, etc.
The service temperature of ASTM A179 high temperature boiler tube depends on the material and specification of the steel tube. Typically, the service temperature range of this type of steel pipe is -200°C to 450°C. Within this temperature range, steel pipes can maintain good mechanical properties and corrosion resistance. It should be noted that the actual use temperature should be selected according to specific equipment and process requirements to ensure the safety and reliability of the steel pipe.
It offers three levels:
Grade A – Mild Steel
Grade C - medium carbon steel
Grade D - carbon manganese steel
ASME Standard Example: ASME SA192 Boiler Tube
SA192 is a material, specifically, it is a standard used for manufacturing high-pressure boiler tubes. This pipe performs well in high-pressure environments due to its excellent tensile strength and yield strength, as well as good elongation, and is able to withstand large pressures and stresses. The chemical composition of SA192 steel pipes is strictly controlled and mainly includes elements such as silicon, manganese, chromium, molybdenum, copper and nickel. The content of these elements has an important impact on the performance and quality of the pipe. In addition, SA192, together with SA-193 and SA-194, is classified as a standard for stainless steel, stainless iron or alloy steel.
Commonly used materials for boiler tubes:
Boiler tubes are usually made of carbon steel, stainless steel and alloy steel tubes. Their differences are shown in the table below.Attribute | Carbon Steel Boiler Tubes | Stainless Steel Boiler Tubes | Alloy Steel Boiler Tubes |
---|---|---|---|
Chemical Composition | Iron and carbon, low carbon content (<0.35%) | At least 10.5% chromium, often with nickel, molybdenum | Iron, carbon, and various alloying elements (e.g., manganese, silicon, chromium, nickel) |
Mechanical Properties | Lower strength and hardness | Good formability; moderate strength | Higher strength, toughness, and wear resistance |
Corrosion Resistance | Low; may need coatings or linings | High due to chromium oxide layer | Good to excellent, depending on alloying elements |
Applications | General-purpose, low to moderate temperature and pressure | Corrosive environments, food processing, chemical industry | High-temperature and high-pressure applications, such as in power stations |
Cost and Economy | Lower initial cost; may require more maintenance | Higher initial cost; potentially lower lifecycle cost | Varies; can be more expensive due to alloy content |
Environmental Impact and Sustainability | Regular maintenance may be needed | Recyclable; low maintenance | Varies; some alloys are highly recyclable |
Lifespan | Shorter lifespan if not properly protected against corrosion | Longer lifespan due to self-healing properties and corrosion resistance | Long lifespan, especially in harsh environments; depends on alloy composition |
Boiler tube components and materials used:
Boiler Component | Function Description | Typical Material Used |
---|---|---|
Water Wall Tubes | Main heat-receiving surface around the furnace. | Carbon Steel |
Convection Tubes | Further heating of fluid in the convection area of the boiler. | Carbon Steel or Alloy Steel |
Downcomer Tubes | Transport water from the steam drum to the downcomer. | Carbon Steel |
Header (Collector) | Collects and distributes boiler water; not typically exposed to radiant heat. | Carbon Steel or Stainless Steel |
Superheater Tubes | Heat saturated steam into superheated steam, improving steam quality. | Alloy Steel |
Economizer Tubes | Use residual heat from exhaust gases to raise feedwater temperature. | Carbon Steel or Alloy Steel |
Go here to learn more about "How are Seamless Boiler Tubes Made?"