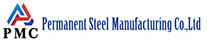
Drill pipe is an important part of the oil and gas industry, used to transfer drilling fluid and apply rotational force to the drill bit during drilling operations. The manufacturing process of drill pipe involves multiple steps to ensure its durability and functionality in harsh drilling conditions. Here's an overview of the typical drill pipe manufacturing process:
Material Selection
Drill pipes are typically made from high-strength steel. The steel grade is chosen based on the required mechanical properties like tensile strength, yield strength, and toughness. Commonly used materials include AISI 4145H and AISI 4140.
Cutting and Forming
The first step involves cutting the raw material into appropriate lengths, which are usually around 30 feet (9 meters). These lengths are then heated to a specific temperature to make them malleable for further processing. The heated lengths are formed into tubes using a combination of mechanical processes like hot rolling or extrusion.
Heat Treatment
After forming, the tubes undergo heat treatment processes like quenching and tempering to improve the mechanical properties of the steel, such as toughness and strength. This process also relieves any residual stresses introduced during forming.
Threading and Upsetting
The ends of the drill pipe are threaded to connect with other components of the drill string, such as the drill bit and the bottom hole assembly. The threading process involves cutting the threads onto the pipe ends using specialized threading machines. After threading, the ends are usually upset (swelled) to increase their wall thickness, making them more robust and able to handle the stress of drilling operations.
Inspection and Testing
Each step of the manufacturing process involves rigorous quality control and inspection. This includes ultrasonic testing, magnetic particle inspection, and other non-destructive testing methods to detect any defects or irregularities that could compromise the integrity of the drill pipe. Each pipe is tested under high pressure to ensure it can withstand the pressures it will encounter during drilling operations.
Hardbanding
Drill pipes are susceptible to wear, especially near the tool joints where they make contact with the wellbore. To mitigate wear and extend the life of the drill pipe, a hardbanding process is often applied. This involves welding wear-resistant materials onto specific areas of the pipe.
Finishing and Coating
The pipes are coated with a protective layer to prevent corrosion during storage and transport. This coating could be a rust inhibitor or a layer of paint.The pipes are marked with identification numbers, grade, and other specifications for traceability.
Final Inspection and Certification
A thorough inspection is conducted to ensure all dimensions, threads, and mechanical properties meet the required standards.
The pipes are certified according to industry standards (e.g., API 5DP).
Packaging and Shipping
The drill pipes are bundled, typically with protective caps on the threads, and are prepared for shipping to drilling sites.
This comprehensive process ensures that drill pipes are manufactured to meet the demanding conditions of drilling operations, providing reliability and safety in the field.
Read more: Common Drill Pipe Connection