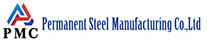
The 316L stainless steel welded pipe is a pipe made of 316L stainless steel through welding process. Common forming processes include cold rolling and hot rolling.
It is a kind of stainless steel pipe, which is widely used in many fields and meets various engineering and industrial needs with its excellent performance characteristics. The quality inspection standards for 316L stainless steel welded pipes mainly include the following aspects:
1. Chemical composition test
Standard requirements: The main chemical composition of 316L stainless steel welded pipes should meet the corresponding standards, such as carbon content ≤0.03%, silicon content ≤1.0%, manganese content ≤2.0%, chromium content 16.0%-18.0%, nickel content 10.0%-14.0%, molybdenum content 2.0%-3.0%, sulfur content ≤0.03%, phosphorus content ≤0.045%.
Inspection method: Spectral analysis and other methods are usually used to detect the chemical composition of the welded pipe to ensure that the content of each element is within the specified range, thereby ensuring that the corrosion resistance and mechanical properties of the welded pipe meet the requirements.
2. Dimensional accuracy inspection
Outer diameter and wall thickness: The outer diameter and wall thickness of the welded pipe should comply with the tolerance range specified in the relevant standards. For example, the common outer diameter tolerance may be around ±0.5%, and the wall thickness tolerance is around ±10%. The specific values will vary depending on the specifications of the pipe and the application field.
Length: The allowable deviation of the general fixed length is ±20mm, and it can also be inspected according to specific contract requirements.
Straightness: The straightness tolerance is usually no more than a certain value per meter, such as 1.5mm/m, to ensure the flatness and straightness of the welded pipe during installation and use.
Ovality: Ovality should be controlled within a certain range, such as not exceeding 80% of the outer diameter tolerance, to ensure the shape accuracy of the welded pipe and prevent the connection and performance of the pipe from being affected by excessive ovality.
3. Appearance quality inspection
Surface defects: The outer surface of the welded pipe should be smooth, without obvious cracks, scars, indentations, scratches, pores, slag inclusions and other defects. Slight indentations that do not exceed the negative deviation of the wall thickness are allowed. The weld on the inner surface of the pipe is allowed to have slight wall thickness increase and weld burrs, but it should meet the requirements of the corresponding standards.
Weld appearance: The weld should be continuous and uniform, without undercut, incomplete penetration, lack of fusion, pores, cracks and other welding defects. The weld height should be controlled within the specified range, generally not exceeding 3mm, and the weld surface should have a smooth transition with the parent material surface.
4. Mechanical properties test
Tensile strength: The tensile strength of 316L stainless steel welded pipe should not be lower than the value specified in the corresponding standard, usually between 480MPa-550MPa. The specific value depends on the size of the pipe, processing technology and application requirements.
Yield strength: The yield strength is generally not less than 177MPa. The yield strength directly affects the load-bearing capacity and deformation performance of the welded pipe during use.
Elongation: The elongation should be no less than 40%, which reflects the plastic deformation ability of the welded pipe during the tensile test. The higher the elongation, the better the toughness of the welded pipe and the better it can adapt to complex stress environments.
5. Nondestructive Testing
X-ray flaw detection: X-rays penetrate the welded pipe to detect defects inside the weld, such as pores, slag inclusions, cracks, etc. The weld quality grade is assessed based on the flaw detection results. Generally, the internal quality of the weld is required to reach Grade II or higher standards.
Ultrasonic testing: Utilize the propagation characteristics of ultrasonic waves in welded pipes to detect defects inside welds and parent materials, locate, quantitatively and qualitatively analyze the detected defects, and ensure that the internal quality of welded pipes meets the use requirements.
Eddy current flaw detection: It is suitable for detecting defects on the surface and near the surface of welded pipes, such as cracks, pores, etc. The existence and location of defects can be determined by detecting the changes in eddy currents. Eddy current flaw detection has the characteristics of fast detection speed and high sensitivity.