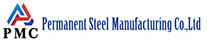
4. stainless steel welded wire used in welding wire must have a dedicated welding material library to ensure that its storage temperature of not less than 18 ° C, humidity is not greater than 60%.
Key details of stainless steel welded pipe production
1. Raw material control: Strictly check the composition, thickness tolerance and surface quality of the stainless steel strip to avoid defects such as inclusions and cracks, and ensure that the material meets the corresponding standards (such as 304, 316).
2. Forming process accuracy: Control the gap between the roller molds during coil forming to ensure the roundness and straightness of the tube diameter and prevent elliptical deformation; adjust the position of the guide wheel to ensure stable feeding of the steel strip and reduce misalignment.
3. Optimize welding parameters: Select welding methods (such as TIG, MIG or high-frequency welding) according to wall thickness, accurately adjust current, voltage and welding speed to avoid incomplete welding, weld nodules or burn-through, and ensure uniform and smooth welds.
4. Weld seam treatment: Clean the surface welding slag and oxide scale in time after welding, and use grinding, pickling or polishing to eliminate the weld excess height to improve the surface finish and corrosion resistance.
5. Online inspection: Use eddy current testing, water pressure testing and other means to inspect the sealing and internal defects of each weld and eliminate unqualified products; measure the pipe diameter and wall thickness to ensure that the dimensional tolerance meets the requirements.
6. Post-processing specifications: The finished product is subjected to solution annealing to eliminate welding stress; passivation treatment is performed to enhance corrosion resistance, and contact with carbon steel is avoided during storage to prevent iron ion contamination.