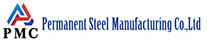
Oil drill pipe is an indispensable tool in the process of oil field exploitation, mainly used for drilling, coring, oil testing and other operations. According to the material, structure and purpose of the drill pipe, it can be divided into the following categories:
1. Steel pipe drill pipe
Steel pipe drill pipe is a drill pipe made of high-strength seamless steel pipe, which is mainly suitable for conventional drilling operations. It is characterized by simple structure and easy maintenance and replacement, but due to the limited strength of the steel pipe, it cannot be used for deeper drilling operations.
2. Non-plug-in drill pipe
Non-plug-in drill pipe is composed of multiple sections of seamless steel pipes, and each section is connected together by a connecting rod. The characteristics of this drill pipe are that it can be used for relatively deep drilling and has good durability. However, due to the existence of the connecting rod, it is not conducive to the seamless connection of the work process, and careful operation is required to achieve the desired effect.
3. Rotary drill pipe
The characteristic of the rotary drill pipe is that it is composed of multiple drill pipes and equipped with a turntable to control the rotation of the drill pipe. This drill pipe is suitable for complex operations such as deep wells and directional wells, and has a high degree of control performance. However, due to its complex structure, it is difficult to maintain.
4. Spiral Drill Pipe
Spiral drill pipe is made of multiple sections of drill pipe without connection by adopting spiral design. It has the characteristics of high strength, high durability and anti-torque. It can be applied to complex working conditions such as deep wells and high-pressure wells, and has efficient and stable working performance. However, due to the difficulty of manufacturing, the cost is relatively high.
What kind of problems will occur to oil drill pipes if they are used improperly?
Improper usage not only affects the service life of the drill pipe, but may also have a serious impact on the safety and efficiency of drilling operations.
1. Excessive use, exceeding the load-bearing capacity of the drill pipe, and operating under harsh geological conditions will cause the drill pipe to break or bend, directly leading to interruption of drilling operations, increasing maintenance and replacement costs, and may even cause safety accidents.
2. Working under high-speed rotation and friction for a long time without necessary lubrication and maintenance will cause serious wear on the surface of the drill pipe, reduce its service life, and increase resistance and energy consumption during drilling.
3. If the torque is too large or too small during connection, the thread is not cleaned, or not enough thread oil is applied, the thread will be damaged, resulting in loose connection of the drill pipe, oil leakage, air leakage, etc., and in severe cases, it may even cause the drill pipe to fall off.
4. If the sealing surface is not cleaned or the sealing material is aged or damaged, it will cause drilling fluid leakage, affect the normal progress of drilling operations, and increase drilling costs.
5. Failure to take effective protective measures when operating in a corrosive environment and improper drilling fluid composition will cause corrosion on the surface and inside of the drill pipe, reducing its strength and toughness and increasing the risk of fracture and failure.
Countermeasures for improper use of oil drill pipes
In order to avoid the situation caused by improper use of oil drilling pipe, measures should be taken:
1. Reasonable selection of drill pipe: Select the appropriate drill pipe type and specifications according to the actual needs of the drilling operation.
2. Standard operation: Connect, disassemble and use the drill pipe strictly in accordance with the operating procedures.
3. Regular maintenance: Regular inspection and maintenance of the drill pipe, including cleaning, lubrication, replacement of damaged parts, etc.
4. Strengthen protection: Take necessary protective measures when working in a corrosive environment, such as adding deoxidizers and buffers.
5. Safety training: Provide safety training to operators to improve their safety awareness and operating skills.
Read more: Precautions for Oil Drill Pipes and Extension of Service Life