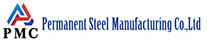
The seamless tube is processed into a capillary tube by a punching machine or an extruder, and then rolled and formed by a rolling mill. The small-diameter tube and the thin-walled tube are subjected to repeated cold rolling-annealing process. Common natural injuries to the seam tube include longitudinal cracking, transverse cracking, folding of the inner and outer walls, and warping, pitting, pitting, and delamination.
The seamlessness of the welded pipe is mainly through heating and reduction rolling.The process of pickling, lubrication, cold drawing heat treatment and heat annealing produces seamless steel pipes. The production of such steel pipes also inevitably has welding problems such as weld seam welding, inclusion and overheating.
Cracks are the most common natural defect, whether welded steel tubes, seamless steel tubes or seamlessness tubes.In the production of steel pipes (welded pipes, seamless pipes or seamless steel pipes), a small number of defective products are inevitably produced. Although the proportion of these defective pipes is not large, it will cause serious consequences in practical applications.
The classic steel pipe inspection method is a hydraulic test method, which is intuitive and simple, and the operator can be employed without any training. However, this method has a large area, high energy consumption and low efficiency.
Most of the early eddy current testing uses the wave height comparison method, that is, only the magnitude of the detected eddy current signal is used to judge whether the steel tube has defects. With the passage of time, people have made in-depth analysis of the results of eddy current flaw detection, and gradually realized the shortcomings of the early common eddy current testing equipment and the wave height comparison method.
The specific performance is that there is a phenomenon of high error detection and missed detection rate. The reason is that this type of eddy current equipment only checks and describes the one-dimensional information of defects, and the research on the sensor is not deep enough, which affects the final result of eddy current testing.
The eddy current flaw detection of steel pipe can not only replace the hydrostatic test, but also the advantages of eddy current flaw detection, such as low investment, quick effect, convenience, safety, fastness, high reliability compared with hydraulic pressure test, small site occupation and low energy consumption.