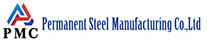
The most serious problem faced by stainless steel pipes in soil and water treatment applications is the corrosiveness of the medium. Soil corrosivity is usually classified by its resistivity. Experiments have shown that if the pH of the soil is greater than 4.5 and there is clean drainage and backfill, 304 and 316 stainless steel will basically not corrode when the soil resistivity is above 2000 ohms/cm.
Like other environments, the chloride content associated with pitting and crevice corrosion may also affect the performance of stainless steel in soil. When it is expected to be inland or non-tidal coastal areas but with higher chloride content, 316 stainless steel is more suitable. For coastal areas and other situations where greater soil resistance may be applied, 2205 duplex or super stainless steel can be considered. If necessary, external protection can be used, such as appropriate protective shells or tapes (pay attention to ensure effective overlap to avoid crevice corrosion), and stainless steel can also be cathodically protected.
When stainless steel pipes are used in water supply and wastewater treatment, 304 stainless steel and 316 stainless steel are generally suitable. They usually do not become thinner during use, so no corrosion allowance is required. This allows the manufacture of thin and light stainless steel pipe products that are easy to transport, and the maintenance requirements are also low during the long service life. They can withstand flow rates of more than 30m/s and perform well under turbulent conditions. Stainless steel pipes do not require chemical additives to be added to the water to maintain the corrosion resistance of the material, and the metal leaching rate is also minimal.
If the stainless steel pipe corrodes completely in water, it is most likely in the form of crevice corrosion. Experiments have shown that when the chloride level is less than 200ppm and 1000ppm respectively, the probability of crevice corrosion of 304 and 316 stainless steel is very low. However, in the design, manufacturing and use, it is still necessary to avoid the appearance of crevice as much as possible, which will help to further reduce the probability of crevice corrosion.
Also consider 1000-3600 ppm chloride 2205 duplex stainless steel. If the service conditions are particularly severe, austenitic or super duplex stainless steels containing 6% molybdenum should be considered. These stainless steels can be used in seawater applications where chloride levels can be as high as 26,000 ppm.
Other good practices are to use L-grade welding, have full penetration welding, and remove surface contamination and heat coloring. After the hydrostatic test, the water should be drained in time, and the ambient medium is in flowing conditions to help keep the surface clean. In addition, overchlorination should be avoided, and sodium hypochlorite or ferric chloride should be added to the metal wall instead of flowing into the flow stream where it can be fully mixed. Areas where chlorine vapor can collect should be regularly flushed with potable water to prevent concentrated chlorides.
Read more: Difference Between 304 and 316 Stainless Steel