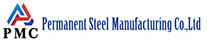
Steel production process:
1. The source of the steel pipe
The source of steel is iron ore, which is the form of iron element (Fe) in nature. Pure iron does not exist in nature. Iron ore is mainly divided into magnetite, hematite and limonite. species, these are oxides of iron, the difference lies in how they are oxidized. The higher the iron content in iron ore, the better. Theoretically, the highest iron content in iron ore is about 72%, and the iron content above 60% is called iron-rich ore. Iron ore is first reduced into iron (milled iron) in the furnace, and then sent to the steelmaking furnace for decarburization and refining into steel. Scrap steel can also be smelted and regenerated in the steelmaking furnace.
General steel is made into products of different properties and shapes according to the purpose of use, which are so-called steel products. Steel products in a broad sense include cast iron, cast steel, forged steel products and processed steel products. Before discussing the raw materials of steel, we must first figure out what is the difference between steel and iron? Are there different ingredients?
In daily life, people always refer to steel and iron together as "steel". It can be seen that steel and iron should be a kind of substance; in fact, from a scientific point of view, steel and iron have a little Different, their main components are all iron, but the amount of carbon contained is different. We usually call "pig iron" with a carbon content above 2%, and "steel" with a carbon content below this value. Therefore, in the process of smelting iron and steel, iron-containing ore is first smelted into molten pig iron in a blast furnace (blast furnace), and then the molten pig iron is put into a steelmaking furnace to be refined into steel. Then, steel (steel billet or strip) is used to make steel pipes, for example, carbon steel billets can be made into steel pipes with hollow sections through hot rolling and cold rolling processes (seamless tubes)
The manufacturing process of seamless steel tubes is mainly divided into two major steps:
1. Hot rolled seamless steel tube: round tube billet → heating → piercing → three-roll cross rolling, continuous rolling or extrusion → stripping → sizing (or reducing) → cooling → straightening → hydraulic test (or flaw detection) → marking → warehousing
2. Cold drawn (rolled) seamless steel tube: round tube blank→heating→piercing→heading→annealing→pickling→oiling (copper plating)→multi-pass cold drawing (cold rolling)→blank tube→heat treatment→straightening → hydrostatic test (flaw detection) → marking → storage.