Analysis and comparison of eddy current testing (ET) and magnetic flux leakage testing (MFL) of seamless tube(SMLS):
With the development of the national economy, all kinds of seamless tubes are widely used in petrochemical and boiler manufacturing industries, especially in harsh working conditions such as high temperature and high pressure, which have higher requirements for the quality of seamless steel tubes. Seamless steel tubes are generally made through the processes of smelting, pouring, billet opening, rolling and drawing. In addition to the various metallurgical defects brought about by the slab, during the forming process, the defects become circumferential points extending along the axial direction of the pipe. In addition to layered defects, in the production process at each stage, cracks, folding, warping, scratches or strains on the surface and interior of the steel pipe will also be caused by improper processing operations, improper design of rolls or drawing dies, etc. defect. In order to ensure the quality of seamless steel tubes, according to relevant product technical standards, surface and internal non-destructive testing must be carried out on the seamless steel tube production line. At present, two technologies, eddy current flaw detection and magnetic flux leakage flaw detection, are often used in the non-destructive testing of seamless tubes. They each have their own characteristics and scope of application.
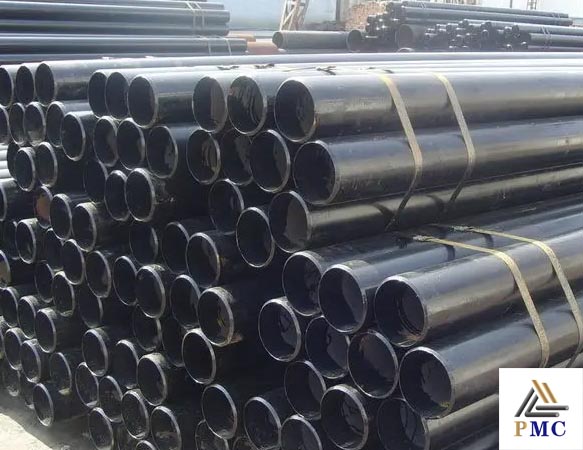
1. Comparison of working principle and characteristics of flaw detection
1.1 Principle and characteristics of eddy current testing
Eddy current testing is a non-destructive testing method based on electromagnetic induction. It excites the probe coil with a sine wave current. When the probe is close to the surface of the seamless steel tube, the alternating magnetic field around the coil generates an induced electromotive force on the surface of the steel pipe to generate induction. current, eddy current. The eddy current generates an induced magnetic field to act on the coil, thereby changing the electrical parameters of the coil. The loss resistance of the eddy current channel and the anti-magnetic flux generated by the eddy current are reflected to the probe coil, changing the current magnitude and phase of the coil, that is, changing the impedance of the coil. The probe moves relatively on the surface of the seamless tube, and when it encounters a defect, the reaction of the eddy current magnetic field to the coil is different, causing a change in the coil impedance, thereby measuring this change to identify the surface defect of the seamless steel tube. Eddy current testing is one of the testing methods that can replace hydrostatic testing. All conductive seamless steel tubes, whether ferromagnetic or non-ferromagnetic, can be tested by eddy current method as long as the outer diameter is greater than 2mm and the wall thickness is not less than 0.1mm. The results of eddy current flaw detection can be directly output as electrical signals, which is easy to realize automatic flaw detection. Eddy current flaw detection adopts non-contact method, and the flaw detection speed is very fast. However, the detectable defect depth of eddy current testing is limited, generally not greater than 5mm, and the test results are often affected by the function of the testing instrument and testing conditions.
1.2 Principle and characteristics of magnetic flux leakage testing
The basic principle of magnetic flux leakage flaw detection for seamless steel tubes is based on the high magnetic permeability of ferromagnetic materials. After ferromagnetic seamless steel tubes are magnetized, their surface and near-surface defects form leakage magnetic fields on the surface of seamless steel tubes. , the presence of defects can be detected by detecting the leakage magnetic field change signal. The magnetic permeability of the defect in the seamless steel tube is much smaller than that of the steel pipe. When the seamless steel tube enters the steel pipe detection line in an assembly line and passes through the detection area quickly, it will be magnetized by the transverse and longitudinal magnetic fields generated by the DC coil. If the seamless steel tube has no defects, most of the magnetic force lines pass through the seamless steel tube, and the magnetic force lines are evenly distributed at this time; if the seamless steel tube is defective, the magnetic force lines are bent, and some of the magnetic force lines leak out of the seamless steel tube surface. Use the transverse and longitudinal probe coils (sensors) to detect the leakage magnetic field escaping from the surface of the seamless steel tube, and then convert the leakage magnetic field into a defect signal (the induced voltage generated by the detection coil in the probe) according to Faraday's law of electromagnetic induction, and further process the defect signal and analysis, you can judge whether there is a defect and the size parameters related to the defect.
2. Comparison of pipeline detection methods
The pipeline eddy current flaw detection uses the penetrating coil method for the flaw detection of the outer surface, and uses the interpolation coil method for the flaw detection of the inner surface. There are two methods commonly used for external surface flaw detection: the coil is fixed to be inspected and the seamless steel tube is fed axially and the coil is fixed to be inspected. The mechanical transmission of flaw detection equipment is relatively simple. The commonly used methods for pipeline magnetic flux leakage flaw detection include two methods: the probe rotates the seamless steel tube to move straight forward and the probe fixes the seamless steel tube to move forward spirally. The mechanical transmission device of the flaw detection equipment is relatively complicated.
3 Detection performance comparison
3.1 Detection range
Eddy current testing is suitable for surface detection of seamless steel tubes of various conductive materials, no matter whether the seamless pipe is ferromagnetic or non-ferromagnetic, and whether it is ferrous metal, non-ferrous metal or non-metal, as long as the seamless steel tube is conductive If the outer diameter and wall thickness meet certain conditions, the eddy current method can be used for testing. It is more suitable for the detection of outer surface defects of ordinary thin-walled seamless steel tubes, and is widely used in the detection of surface defects of seamless steel tubes such as carbon steel, alloy steel pipes and stainless steel. Magnetic flux leakage detection is only suitable for the detection of ferromagnetic seamless steel tubes, and it can detect the inner and outer surface defects of seamless steel tubes. This method is more suitable for the detection of large-diameter thick-walled ferromagnetic seamless pipes.
3.2 Detection sensitivity
It can be seen from the basic characteristics of eddy current that the eddy current density is mainly distributed near the surface of the conductive material. Therefore, the more surface defects exist in the tested seamless steel tube, the more fully the use of the eddy current effect will be. Therefore, eddy current testing is suitable for the detection of surface defects or near-surface defects of conductive seamless tubes, and the sensitivity is higher than that of magnetic flux leakage testing at this time. For internal defects, due to the "skin effect" in eddy current testing, the eddy current density decays according to the negative exponential law inside the conductive conductor, and the penetration depth decreases with the increase of frequency, electrical conductivity and magnetic permeability. Sensitivity is reduced. Eddy current testing can generally only detect single-sided surface defects (inner surface or outer surface) of seamless steel tubes; magnetic flux leakage testing can detect inner and outer surface defects of seamless pipes at the same time, and has a certain sensitivity to internal defects. Compared with eddy current testing, magnetic flux leakage testing is less sensitive to detecting defects.
4. Signal processing comparison
Both eddy current and magnetic flux leakage testing use corresponding standard reference sample tubes to verify the comprehensive performance of the testing system, set and correct the working parameters and operating conditions of the flaw detector, and compare and evaluate defect signals during testing. These two detection methods display defects in the form of electrical signal output, and the signal processing is more convenient. However, due to different physical principles, the signal processing and sensor structure of the two detection methods are quite different. Because eddy current detection must have high-frequency excitation signals, it brings certain difficulties to signal processing, and it is easy to cause mutual interference of signals, and the signal processing and sensor structure are more complicated. The magnetization of magnetic flux leakage detection can adopt permanent magnet, DC magnetization or AC magnetization. In permanent magnet and DC magnetization, there is no high-frequency signal, and the interference is small, which brings great convenience to signal processing. The signal processing and sensor structure are very simple.
5.Conclusion
To sum up, these two surface online flaw detection methods for seamless steel tubes have their own advantages and limitations, and the seamless steel tube production line can be selected according to the specific situation. Eddy current flaw detection is suitable for flaw detection of various conductive seamless steel tubes, whether it is stainless steel tubes or carbon steel seamless tubes, and the detection is not affected by impurities such as oil stains on the surface of seamless steel tubes. The detection speed is fast and the sensitivity is high. Magnetic flux leakage testing can not only detect internal, external surface and subcutaneous defects, but also can know the characteristic dimensions such as defect depth and length and whether it reaches the set rejection level from the relationship between the established electrical signal amplitude and defect parameters without measurement. Strong detection ability and fast detection speed. But it is only suitable for ferromagnetic seamless steel tubes, the investment in testing equipment is large, and the sensitivity of detecting defects is low.