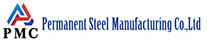
The stainless steel seamless pipe is a long steel strip with a hollow cross-section and no seams around it. The thicker the wall thickness of the product, the more economical and practical it is. The thinner the wall thickness, the higher the processing cost.
The process of this product determines its limited performance. Generally, seamless steel tubes have low precision: uneven wall thickness, low brightness of the inner and outer surfaces of the pipe, high cost of cutting, and pitting and black spots on the inner and outer surfaces are difficult to remove; its detection and shaping must be processed offline. Therefore, it has demonstrated its superiority in high pressure, high strength, and mechanical structure materials.
Inner surface defects
1. Inward fold
Characteristics: Straight or spiral or semi-spiral serrated defects appear on the inner surface of the stainless steel seamless pipe.
Causes:
1) Tube billet: loose center, segregation; serious shrinkage hole residue; non-metallic inclusions exceed the standard.
2) Uneven heating of tube billet, too high or too low temperature, too long heating time.
3) Perforation area: serious wear of the plug; improper adjustment of perforator parameters; aging of perforating rollers, etc.
Inspection: Inner folds are not allowed on the inner surface of the steel pipe. The inner folds at the pipe ends should be ground or re-cut. The actual wall thickness at the grinding point shall not be less than the minimum value required by the standard; inner folds throughout the length are judged as scrap.
2. Internal scarring
Characteristics: The inner surface of the stainless steel seamless pipe shows scarring, which is generally not rooted and easy to peel off.
Causes:
1) Impurities in the graphite lubricant.
2) The iron ear at the rear end of the rough pipe is pressed into the inner wall of the steel pipe, etc.
Inspection: The inner surface of the steel pipe is not allowed to exist, the pipe end should be ground and re-cut, and the grinding depth should not exceed the negative deviation required by the standard;
The actual wall thickness shall not be less than the minimum value required by the standard; the internal scarring of the whole length shall be scrapped.
3. Warping
Characteristics: The inner surface of the steel pipe presents straight or intermittent small skins that are raised in the shape of nails. It often appears at the head of the rough pipe and is easy to peel off.
Causes:
1) Improper adjustment of the perforator parameters.
2) Steel sticking to the head.
3) Iron oxide scale accumulation in the rough pipe, etc.
Inspection: The inner surface of the stainless steel seamless pipe is allowed to have warping without roots that are easy to peel off (or can be burned during heat treatment). Warping with roots should be ground or cut off.
4 Internal straight lines
Characteristics: There are linear scratches with a certain width and depth on the inner surface of the steel pipe.
Causes:
1) The rolling temperature is low and the core rod is stuck with metal hard objects.
2) Impurities in the graphite, etc.
Inspection:
1) The casing pipe and general pipe are allowed to have internal straight lines with a depth not exceeding 5% (the depth of pressure vessels is 0.4mm).
The internal straight lines should be ground and removed.
2) The internal straight lines with sharp edges should be ground and smoothed.
5. Inner edge
Features: There are linear protrusions with a certain width and depth on the inner surface of the steel pipe.
Causes: Severe wear of the mandrel, grinding that is not smooth or too deep, etc.
Inspection:
1) Casings and line pipes are allowed to have inner edges with a height not exceeding 8% of the wall thickness and a height not exceeding 0.8mm that does not affect the diameter. If the tolerance is exceeded, it should be repaired and re-cut.
2) General pipes and line pipes are allowed to have inner edges with a height not exceeding 8% of the wall thickness (height is 0.8mm). If the tolerance is exceeded, it should be repaired and re-cut.
3) For L2 grade (i.e. N5) flaw detection steel pipes, the height of the inner edge shall not exceed 5% (height is 0.5mm). If the tolerance is exceeded, it should be repaired and re-cut.
4) Inner edges with sharp edges should be polished and smoothed.
6. Internal bulge
Characteristics: The inner surface of the steel pipe presents regular convexity and the outer surface is not damaged.
Cause: The continuous rolling roller is over-grinded or the meat is lost, etc.
Inspection: Inspect according to the requirements of the inner edge.
7. Dimples
Characteristics: The inner surface of the steel pipe shows regular or irregular pits and the outer surface is not damaged.
Causes:
1) Improper adjustment of continuous rolling, mismatch of rolling speeds of each stand roller.
2) Uneven heating of the tube billet or too low temperature.
3) Departure of the rolling center line, collision between the steel pipe and the roller after continuous rolling, etc. (Note: This reason was proposed in 2003.1, and the principle is still under discussion).
Inspection: Dimples that do not exceed the negative deviation of the wall thickness and the actual wall thickness is greater than the minimum value of the wall thickness requirement are allowed to exist. Dimples that exceed the standard should be removed. (Note: Severe development of the dent is called cracking, and this kind of damage should be strictly inspected).
8. Internal thread (this defect only occurs in the Assel unit)
Characteristics: There are spiral marks on the inner surface of the steel pipe, which mostly appear on the inner surface of thin-walled pipes, and have an obvious uneven feel.
Causes:
1) Inherent defects of the oblique rolling process. This defect is more prominent when the process parameters of the Assel tube rolling mill are not adjusted properly.
2) The deformation distribution is unreasonable, and the Assel wall reduction is too large.
3) The Assel rolling roller is improperly configured.
Inspection: The depth of the internal thread defect of the steel pipe is not greater than 0.3mm and is within a certain tolerance range.
Read more: How to Maintain and Clean Stainless Steel Seamless Pipes?