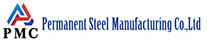
Stainless steel seamless pipe is a long steel strip with a hollow cross-section and no seams around it. The thicker the wall thickness of the product, the more economical and practical it is. The thinner the wall thickness, the higher the processing cost. During its use, quality problems such as leakage and surface cracks are occasionally found. So how can we avoid these quality problems?
Raw material control
Composition inspection: The quality of stainless steel seamless pipes depends largely on the quality of raw materials. For stainless steel billets, their chemical composition must be strictly inspected to ensure that the content of major alloy elements (such as chromium, nickel, molybdenum, etc.) meets the standards. For example, the chromium content of 304 stainless steel should be between 18% and 20%, and the nickel content should be between 8% and 10.5%. Advanced testing methods such as spectral analysis can be used to accurately determine the content of each element to prevent the performance of the pipe from deteriorating due to composition deviation.
Review of quality certification documents: Require raw material suppliers to provide quality certification documents, including material lists, quality inspection reports, etc. Carefully review these documents to confirm that the raw materials are from legitimate sources and that their quality meets relevant standards, such as national standards or industry standards. For imported raw materials, also check whether they meet the corresponding import quality requirements.
Production process control
1. Hot rolling process control (if applicable):
Temperature control: During hot rolling, the billet heating temperature is the key. The billet needs to be heated to a suitable temperature range, which generally depends on the type of stainless steel and the size of the pipe. For example, for 316 stainless steel seamless pipes, the hot rolling temperature may be between 1100-1200℃.
Rolling speed and pressure control: Reasonably adjust the rolling speed and pressure to avoid excessive rolling force caused by too fast rolling speed, which may cause cracks in the pipe or uneven wall thickness.
2. Cold rolling process control (if applicable):
Control of diameter reduction and wall reduction operation: Cold rolling is mainly used for finishing of pipes. During the cold rolling process, the diameter reduction and wall reduction of the pipe must be accurately controlled. The deformation of each cold rolling should not be too large, otherwise it will cause excessive hardening of the pipe and affect its subsequent processing performance.
Dimensional accuracy control: Use high-precision cold rolling equipment and measuring instruments to perform real-time measurement and feedback control of the outer diameter, inner diameter, wall thickness and other dimensions of the pipe.
3. Perforation process control:
Selection and maintenance of piercing needles: Perforation is a key step in manufacturing seamless pipes. Choose a suitable piercing needle whose diameter, shape and material should match the size and material of the pipe. Check and maintain the piercing needle regularly to ensure that its surface is smooth and undamaged, because the quality of the piercing needle directly affects the inner diameter accuracy and surface quality of the pipe.
Punching parameter adjustment: control parameters such as punching speed and punch pressure. The piercing speed is generally adjusted according to the material and size of the pipe to avoid excessive speed causing pipe tearing or quality defects. The head pressure should be moderate to ensure that the center of the billet can be pierced smoothly to form a hollow billet.
Surface quality control
1. Surface treatment process selection: Select the appropriate surface treatment process according to the purpose of the pipe and customer requirements. If it is a seamless stainless steel pipe for decoration, it may need to be polished to make the surface of the pipe as bright as a mirror. If the pipe is used in the chemical industry and other industries, it may need to be pickled and passivated to enhance the corrosion resistance of the pipe.
2. Surface defect inspection and repair: During the production process, the surface quality of the pipe should be checked regularly, and surface defects such as cracks, scratches, pits, etc. should be detected through visual inspection and non-destructive testing. For minor surface defects, grinding, polishing and other methods can be used to repair them; Severe defects, such as deep cracks, may require the pipe to be scrapped or reprocessed.
Quality inspection and recording
1. Application of non-destructive testing technology: Use a variety of non-destructive testing technologies to test the quality of stainless steel seamless pipes.
2. Mechanical properties test: Conduct mechanical properties tests on pipes, including tensile strength, yield strength, elongation, hardness and other tests.
3. Establishment of quality record and traceability system: Establish a complete quality record system to record various parameters in the pipe production process, including raw material information, production process parameters, quality inspection results, etc.
Read more: Stainless Steel Seamless Pipes Specifications and Quality Standards