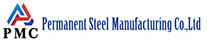
Common problems in high frequency welding and their causes and solutions:
High-frequency welding originated in the 1950s. It is a new type of welding process that uses the skin effect and proximity effect produced by high-frequency current to connect steel plates and other metal materials. The emergence and maturity of high-frequency welding technology has directly promoted the huge development of the longitudinally welded pipe industry. It is a key process in the production of ERW steel pipe. The quality of high-frequency welding directly affects the overall strength, quality level and production speed of welded pipe products.
High-frequency welding is a key process in the production of welded pipes. Due to systemic influencing factors, we still need to explore experience in the first line of production. Each unit has its own design and manufacturing differences, and each operator is also different. The habit of doing things, that is to say, the crew, like people, have their own personalities. We provide these materials to everyone in order for us to better understand the basic principles of high-frequency welding, so as to better integrate our own production practices and summarize the operating procedures suitable for our own units.
Tips: In case ASTM A53 Grade B in ERW (electric resistance welded) pipe, the weld seam shall be done the heat treatment with a minimum 1000°F [540°C]. In this way the no untempered martensite remains.
In case ASTM A53 B pipe in cold expanded, then expansion should not exceed 1.5% of the required OD.