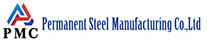
1. 3PE anti-corrosion
3PE anti-corrosion refers to coating the surface of the steel pipe with three layers of polyethylene material, which is divided into a three-layer structure of inner polyethylene (HDPE), middle binder and outer polyethylene (MDPE). 3PE anti-corrosion has excellent waterproof, moisture-proof and anti-corrosion properties, and is suitable for underground pipelines, oil and gas pipelines and other projects.
2. 2PE anti-corrosion
2PE anti-corrosion refers to coating the surface of the steel pipe with two layers of polyethylene materials, including an inner layer of polyethylene (HDPE) and an outer layer of polyethylene (MDPE). 2PE anti-corrosion has good waterproof, moisture-proof and anti-corrosion properties, but compared with 3PE anti-corrosion, its corrosion resistance is slightly inferior.
3. Epoxy coal pitch anti-corrosion coating
Epoxy coal pitch anti-corrosion coating has good weather resistance, wear resistance and chemical corrosion resistance, and can be used for anti-corrosion treatment of steel pipes. Epoxy coal tar pitch anti-corrosion is suitable for water pipes, oil pipes, city gas pipes and other fields.
4. Epoxy powder anti-corrosion
Epoxy powder coating is based on epoxy resin and has good adhesion, weather resistance and chemical corrosion resistance. Epoxy powder anti-corrosion is often used in water pipelines, oil pipelines, chemical pipelines and other fields.
5. Steel pipe zinc coating anti-corrosion
Steel pipe zinc coating anti-corrosion is to form a zinc layer on the surface of the steel pipe through hot-dip galvanizing or electro-galvanizing process, which plays an anti-corrosion role. The zinc layer has good corrosion resistance and adhesion, and is suitable for water pipes, gas pipes, building structures and other fields.
6. Glass flake anti-corrosion
Glass flake anti-corrosion coating contains a large amount of glass flakes and has excellent weather resistance, wear resistance and chemical corrosion resistance. During the coating process of glass flake anti-corrosion coating, the glass flakes will form a dense protective layer, which effectively blocks the intrusion of moisture and chemical substances, thereby extending the service life of the steel pipe. Glass flake anti-corrosion is suitable for anti-corrosion projects in harsh environments such as water pipelines, oil pipelines, chemical pipelines, and offshore platforms.
7. Polyurethane anti-corrosion
Polyurethane coating has excellent weather resistance, abrasion resistance, chemical corrosion resistance and good adhesion. Polyurethane anti-corrosion coating can effectively prevent the intrusion of moisture, oxygen and chemical substances and extend the service life of steel pipes. Polyurethane anti-corrosion is often used in offshore oil pipelines, long-distance natural gas pipelines and other fields.
8. Polypropylene anti-corrosion
Polypropylene anti-corrosion coating has good weather resistance, wear resistance, chemical corrosion resistance and adhesion. Polypropylene anti-corrosion coating can effectively resist the intrusion of moisture, oxygen and chemical substances, extending the service life of steel pipes. Polypropylene anti-corrosion is suitable for water pipelines, oil pipelines, chemical pipelines and other fields.