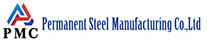
Causes of welding deformation of thin steel plate:
1. Analysis of welding deformation
Welding uses heat to connect two workpieces, but the heat will cause welding thermal deformation of the workpiece. When the workpiece is not uniformly heated, the stress is greater than the yield point of the material, and the workpiece will expand and contract, resulting in residual stress and residual deformation after cooling.
Using continuous spot welding instead of continuous welding can prevent and reduce the damage caused by welding deformation. In addition, the commonly used method is anti-deformation method, using assembly and welding sequence to control deformation, and using assembly and welding sequence to control deformation is also a good method , It is very beneficial for maintenance personnel to improve efficiency and reduce labor intensity.
From the perspective of the effect of segmented welding, welding from the middle to both ends is better than welding from both ends to the middle. The two ends of the steel plate are welded to the middle, and the heat in the middle part is continuously accumulated, which makes the middle part seriously deformed. The sequential welding causes the heat to increase rapidly along the welding direction and continuously reduce the temperature. The same is true for welding from the middle to the ends. The welding of steel plates shall be continuous spot welding in sections from the middle to the ends.
Tips: ERW welded pipe is formed by rolling strip and welding the seam, with tighter dimensional tolerances and less weight. The weld seam is heat treated after welding that no untempered martensite remains, and the weld flash can be removed from both inner and outer surfaces.
ASTM A53 ERW steel pipe is a typical carbon steel pipe. It is largely used to convey fluids at low / medium pressures such as oil, gas, steam, water, air and also for mechanical applications.