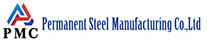
(1) Perforating operations.
Perforating is an essential task before fracturing and acidification. Improper engineering design or operation can also cause damage to the casing. For example, too much hole density reduces the strength of the casing, and perforation causes cement outside the casing. The ring is broken, resulting in casing rupture, the perforation depth is too large or the design is inaccurate, and the interlayer mudstone is mistakenly shot through, causing the mudstone water to expand, resulting in changes in ground stress, resulting in casing deformation or misalignment.
(2) Fracturing and acidification operations.
In the past decade or so, people have adopted large-scale fracturing measures for oil wells to consider the effect of transforming low-permeability oil layers. The wellhead pressure can reach 50-70MPa, and the casing pressure in the oil layer has reached 70-100MPa. The internal pressure resistance strength of commonly used N-80 casing is designed to be 64.6MPa, while the strength of J-55 casing is only 21.93~28.4MPa. In this way, casing couplings and threaded parts and well sections with poor cementing quality are prone to rupture. In addition, when oil wells are acidified, casing corrosion occurs because acid is not discharged in time. Some wells are acidified multiple times, which accelerates the corrosion rate of the casing, causing casing perforation and leakage.
(3) Oil well transfer and downhole tools.
When oil wells reach a later stage of production, some oil wells will be converted into water injection wells. The original oil well cement return height is only about 200m above the oil layer, while the normal water injection well cement return height requirement is to the wellhead. The transfer well is relatively different from the normal water injection well. The height of the cement return is not high enough. The upper casing is not protected by the cement ring and is completely immersed in the shallow water above. On the one hand, there is serious corrosion outside the pipe. On the other hand, the upper casing is subjected to water injection pressure after injection, which promotes each other with the corrosion outside the pipe, aggravating the damage to the casing. In addition, the collision damage of downhole tools to the inner wall of the casing will also aggravate the corrosion, especially when there is a packer downhole, the packer will cause extremely serious damage to the inner wall of the casing. First of all, the strong stress expansion when the packer is seated will cause huge stress damage to the inner wall of the casing; secondly, due to the obstruction of the packer, dirt easily accumulates near the packer, causing corrosion under the scale, and stress damage synergizes with scale. Under the action of stress, the casing loss rate near the packer will increase significantly. When the packer fails and is unsealed, it will cause serious damage to the sealing position. A large amount of practice has proved that the damage to the casing when the packer is unsealed is extremely serious.
2. Internal factors