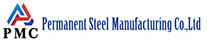
Drill pipes are a critical component in the drilling process, especially in the oil and gas industry. They are long, hollow, and cylindrical pipes used to transmit drilling fluid and rotational power from the drilling rig to the drill bit. Drill pipes are subject to harsh conditions, including exposure to corrosive environments, which can lead to significant wear and damage over time. Implementing anti-corrosion measures is crucial for maintaining the integrity and longevity of drill pipes. Here are some common methods:
1. Protective Coatings
Epoxy Coatings: These are commonly used to coat the inner and outer surfaces of drill pipes, providing a barrier against corrosive substances.
Zinc Coatings (Galvanizing): Zinc offers cathodic protection, meaning it will corrode in place of the steel, thereby protecting the pipe.
Ceramic Coatings: These are used for high-temperature and abrasive environments, providing excellent resistance to corrosion.
2. Use preservatives
In order to prevent corrosion on the surface of the drill pipe, a common method is to spray anti-corrosion agent on the surface of the drill pipe. This method can use both organic and inorganic preservatives. The advantages of organic preservatives are good wear resistance and long service life, but the cost is relatively high. The advantages of inorganic preservatives are low cost and good environmental performance, but they require regular maintenance of the coating.
3. Material Selection
Corrosion-Resistant Alloys: Using alloys such as stainless steel or Inconel for drill pipes can enhance resistance to corrosion, especially in high-chloride environments.
Composite Materials: Pipes made from composite materials like fiberglass are inherently resistant to corrosion.
4. Regular Maintenance and Inspection
Routine Inspections: Regular checks for signs of corrosion allow for early detection and intervention.
Cleaning and Flushing: Regularly cleaning the pipes to remove corrosive agents can help prolong their life.
Repair and Recoating: Applying new coatings or repairing damaged areas can prevent the progression of corrosion.
5. Design Considerations
Optimized Pipe Design: Ensuring proper design that minimizes the exposure of pipes to corrosive agents can help reduce corrosion.
Proper Storage: Storing drill pipes in a dry, controlled environment when not in use can prevent corrosion.
6. Environmental Controls
Controlled Atmosphere: If possible, controlling the atmosphere around the drill pipe (e.g., by dehumidification) can minimize the presence of moisture, a key factor in corrosion.
7. Electroplating
Electroplating is a method of electroplating metal onto the surface of drill pipe. Electroplating can prevent the surface of the drill pipe from being corroded and can also improve the hardness and wear resistance of the drill pipe. Currently commonly used electroplating methods include chromium plating, nickel plating, zinc plating, etc.
Through reasonable maintenance and maintenance measures, the service life and stability of the drill pipe can be guaranteed. Implementing these measures can significantly enhance the service life of drill pipes and reduce maintenance costs.
Read more: Common Drill Pipe Connection